P – 170 - 2021 산소 배관 및 배관설비에 관한 기술지침(KOSHA GUIDE) - 2021.12.
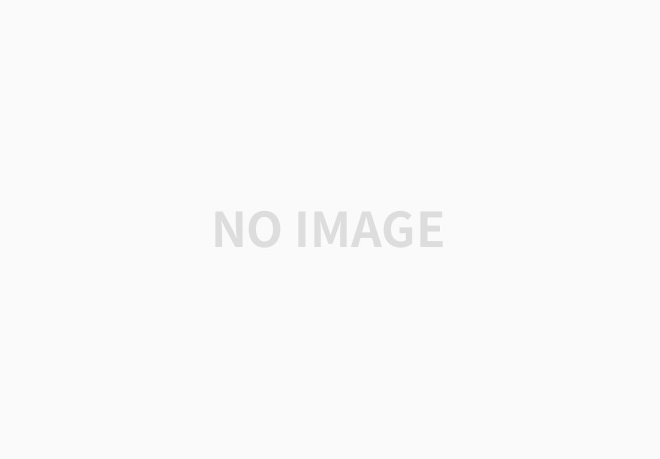
1. 목적
산소를 취급하는 콜드 박스 외부의 공기 분리 플랜트에 있는 금속산소 배관, 분배 배관설비 및 가스 산소배관의 안전을 확보하는데 필요한 사항을 제시하는데 그 목적이 있다.
2. 적용범위
이 지침은 온도범위가 –30∼200°C, 압력이 최대21MPa(3000psig), 이슬점 30℃ 이하인 가스 산소에 대하여 적용한다. 다만, 산소 실린더 충전플랜트, 의료용 산소배관설비, 콜드박스 내부배관, 산소압축장치, 액체 산소 기화기, 대용량 산소설비(액제 산소 또는 고압가스) 및 기계배관은 제외 한다.
3. 정의
3.1 “산소배관”이라함은 산소를 사용하는 설비로 배관 및 구성요소을 말한다.
3.2 “플랜트 파이프(Plant piping)”라함은 산소생산 시설 내의 배관을 말한다.
3.3 “가스 산소(Gaseous oxygen)”라함은 부피기준 23.5% 이상의 산소를 포함하는 가스를 말한다.
3.4 “저순도 산소(Low purity oxygen)”라함은 부피기준 산소의 농도가 23.5∼35%의 산소를 포함하는 가스를 말한다.
3.5 “고순도 산소(Standard purity oxygen)”라함은 부피 기준산소의 농도가 99.5% 이상의 산소를 포함하는 가스를 말한다.
3.6 “초고순도 산소(UHP, Ultra-high purity oxygen)”라함은 부피 기준산소의 농도가 99.999% 이상의 산소를포함하는 가스를 말한다.
3.7 “가스 압력(Gas pressure)”이라 함은 배관 및 배관설비 내에서 달성할 수 있는 최대압력을 말한다.
3.8 “유속(Velocity)”이라 함은 실제 체적을 단면적으로 나눈값을 말하며, 파이프와 그 구성요소의 유속을 크게 다룰수 있다.
3.9 “면제재질(Exempt materials)”이라 함은 정의된 압력, 재질두께 및 산소순도 한계 내의 산소속도 제한에서 면제되는 엔지니어링 합금을 말한다. 부록1,2는 특정합금의 구성요소와 두께 제한 및 산소설비내의 면제압력을 말한다.
3.10 “면제압력(Exemption pressure)”이라함은 입자충돌이 발생할 수 있는 산소가 풍부한 조건에서 재질에 속도제한이 적용되지 않는 최대압력을 말한다. 부록2에 나열된 합금의 면제압력은 업계경험과 ASTM G124,“산소에서 엔지니어링
재질의 연소거동을 결정하기 위한 표준테스트 방법”에 따른점화 연소시험의 조건을 기반으로 작성된 것이다.
3.11 “건조 오일 프리 공기 또는 질소(Dry, oil-free, airornitrogen)”이라함은 이슬점이 –40℃ 이하 이고, 오일 함량이 0.5㎎/㎥ 이하인 공기 또는 질소를 말한다.
3.12 “내화성 합금(Burn resistant alloys)” 이라함은 점화된 후에도 불이 붙거나 타지않는 엔지니어링 합금을 말한다. 산소순도, 온도 및 최소 재질 두께를 포함하여 정의된 일련의 공정조건에서 사용된 면제압력 이하의 금속은 내화성 합금으로 간주 한다.
3.13 “코발트 합금(Cobalt alloys)”이라함은 일반적으로 최소 40% 중량의 최소 코발트를 함유한 합금을 말하며, Stellite 6 또는 Stellite 6B와 같은 내마모성 합금은 때때로 침식 손상을 최소화하고 밸브 수명을 개선하기 위해 밸브 트림의 코팅으로 사용된다.
3.14 “구리 합금(Copper-based alloys)”이라함은 일반적으로 최소 55% 중량 이상의 구리를 함유한 합금을 말하며, 산소 배관 및 배관 설비용 부품에 사용 된다. 대표적인 예로는 구리, 황동(주로 아연으로 합금된 구리), 청동(알루미늄,실리콘, 망간, 주석, 납 등으로 합금된 구리) 및 구리 니켈(니켈로 합금된 구리) 등이 있다.
3.15 “철 합금(Ferrous alloys)”이라함은 탄소강, 저합금강 및 모든 스테인레스 강이 포함되고, 주조 또는 단조형태로 사용한다.
3.16 “니켈 합금”이라함은 최소 50% 중량에서 최대 99% 중량의 니켈 함량을 함유하는 니켈 기반 합금을 말하며, 주로 산소가스 전송용 파이프 라인 및 배관 설비에사용된다. 일반적으로 함유된 니켈 및 구리함량이 높을수록 합금의 내화성이높아진다.
3.17 “비철 합금(Non-ferrous alloys)”이라함은 구리, 니켈 및 코발트만 포함된 합금을 말하며, 알루미늄, 지르코늄 등과 같은 반응성 물질은 제외된다.
4. 안전설계
4.1 일반사항
(1) 산소 이송 파이프 라인 또는 배관설비의 안전한 설계 및 운전은 서로 영향을 미칠 수 있는 다양한 요인이 있다.
(2) 산소는 화재 3요소의 산화제 중에서 아주 강한 산화제에 속한다.
(3) 산소 설비에서 산소는 산화제이며 농도, 압력, 온도 및 유량이 증가함에 따라 배관 설비의 화재위험이 증가한다.
(4) 산소 설비의 연료는 구성 재질(금속, 비금속 및 윤활유) 또는 미립자,오일 또는 그리스와 같은 오염물질 등이다.
(5) 산소 설비에 공통적인 점화원에는 이물질에 의한충격, 단열압축, 마찰가열 등이 있다.
(6) 산소 설비는 운전조건에 따라 화재의 3요소가 공존할 수 있어 화재폭발의 위험이 아주 높아 어떠한 경우도 항상허용 가능한 수준 이하로 설계, 운전 및 유지보수가 되어야 한다.예를 들어, 산화제의 심각도를 최소화 하는것은 실제적으로 산소압력, 온도 또는 농도를 줄이는것이 포함될 수 있다.
(7) 연료의 심각도를 최소화하려면 활성점화 메커니즘이 있는 위치에서 내화성 합금을 사용하도록 보장하는것 이다.
(8) 점화원의 심각도를 최소화 하려면 이물질의 입자 영향을 줄일 수 있도록 산소 설비의 세척, 온도상승 방지를 위하여 압축 열제거, 낮은 유속 등의 안전한 조치를 하여야 한다.
(9) 따라서 모든 구성요소를 포함하여 산소 배관 전송 또는 분배배관은 다음 조건을 고려하여 안전하게 설계하여야 한다.
(가) 산화제 : 유체순도, 조성, 가스 속도, 압력, 온도 및 이슬점과 관련된 산소서비스 조건
(나) 연료-구성재질, 금속 및 비금속 구성 요소 선택, 내화성
(다) 점화원 : 밸브 등의 급속 개방으로 구성 요소에서 이물질 입자 충돌 점화, 마찰 가열 또는 단열 압축 가열에 기여하는 요인(가스 속도 및 충돌 지점 등)
(10) 기타 추가적으로 고려할 사항은 다음과 같다.
(가) 설치환경(예 : 내진설계 등급, 지질 등)
(나) 압력용기, 배관등의 설계 기준
(다) 산소 설비에 관련된 국내외 법규, 관련 규정 등
(라) 산소 설비의 세척 기준 등
(11) 낮은 압력의 산소 설비는 플라스틱 또는 복합재질과 같은 비금속재질을 사용할 수 있다. 그러나 생산공장, 이송배관설비 또는 분배 배관설비에서 산소가 풍부한 가스에 비금속 배관을 사용하는 것은 이 지침을 벗어나며 특정 위험성평가 및 평가결과에 따라서 적절한 조치를 하여야 한다.
(12) 일반적으로 배관과 파이프 라인을 통해 운반되는 기체 산소에는 수분이 포함되어 있으나, 무시할 수 있는 양이기에 부식에 대한 특별한 예방 조치가 필요하지 않다. 그러나 장비 고장(예 : 압축기 인터쿨러 또는 애프터 쿨러)의 경우 배관 및 배관설비가물로오염될수 있는영역을식별할 수 있도록 적절한 설계 및/ 또는 모니터링절차를도입하여야한다.
(13) 습식 산소를 지속적으로 이송하는 경우에는 배관 및 배관 설비 내에 물이 생성될 수 있어 내식성 재질을 사용하거나 내부코팅과 같은 방식 조치를 하여야 한다.
(14) 산소설비에 사용하는 내부코팅, 부식 억제제 등은 산소와 호환성이 있어야 하고, 가연성물질은 사용할 수 없다.
4.2 산소설비의 재질 호환성 산소 설비의 재질선정은 여러 운전조건에 따라 달라질 수 있으며, 일반적으로 재질의 호환성은 재질의 가연성과 점화성(Flammability and ignitability)에 따라 달라진다.
4.2.1 재질의가연성
(1) 재질의 가연성을 결정하는 요소 중 일부에는 재질구성, 두께 및 산소압력, 온도, 농도 등과 같은 작동조건이 포함된다.
(2) 표준테스트 방법은 주로 산소에서 물질의가연성을결정하는데사용되고, 금속의경우 ASTM G 124, 비금속의 경우 ASTM D 2863, 기체 산화제의 액체 및 고체 물질의 경우 ASTM G125 등의 방법을 따른다.
4.2.2 점화 메커니즘과 연쇄 점화
(1) 점화 메커니즘에는 입자충격, 단열 압축(공압충격), 유기물질에 의한 점화 촉진, 마찰가열, 전기아크 등이 있다.
(2) 점화 메커니즘에 대한 특정조건이 존재하면 점화 메커니즘이 활성화된 것으로 간주한다. 예를 들어 입자 충돌이활성화되는데 필요한 조건은 다음과 같다.
(가) 미립자
(나) 높은 가스 속도
(다) 충돌 지점
(3) 이 지침에서 설명된 설계 관행은 점화와 관련된 조건 및 관련 인자를 최소화하기 위한 것이다.
(4) 일단 점화가 되면 가연성 재질과 주위설비는 여러 요인에 따라 주변의 다른 재질을 가열시켜 연쇄적으로 화재가전파될 수 있다.
(5) 화재가 전파되는 속도와 범위는여러가지요인중에서재질의두께와 가연성에따라달라진다.
4.2.3 산소의 정성적 위험성평가 및 정량적 위험성평가
(1) 산소농도, 압력,온도 및 속도와 같은 특정 작동매개 변수는 화재 위험을 증가시킨다.
(2) 이러한 매개 변수가 증가하면, 다음과 같은 보다 엄격한 설계지침이 적용 된다.
(가) 배관 및 장비의 청소 및 청결 유지
(나) 호환 가능한 비금속 및 적절한 경우 윤활유 사용
(다) 면제 재질 사용.
(3) 산소 위험 분석은 산소배관의 화재 위험을 평가하는데 사용되는 방법이다. 또한 점화 가능성 또는 점화 결과 지속성여부를 평가 한다.
(4) 발화 가능성 또는 발화 결과(작동조건에 따라발화 vs. 지속연소)를 평가하며 다음 (5) 내지 (7)에서 자세히 설명한다.
(5) 신규 설계시 재질을 선택하거나 기존 배관설비에 적용할 설계에 필요한 재질을 선정 또는 재질을 변경할때 위험성을 평가하는데 사용할 수 있다.
(6) 금속 합금을 면제 압력이상으로 사용하고 가스 속도가 압력-속도 곡선에 의해 허용된 속도를 초과하는 경우 산소위험 분석이 필요하다.
(7) 위험성평가는 다음과 같은 서로진행한다.
(가) 운전조건(산소순도, 최대운전압력, 온도 및 가스 속도 등)을 검토
(나) 사용하는 재질의 두께 및 코팅하는 물질의 두께와 가연성평가(4.2(1) 참조).
(다) 존재하는 요인에 따라 화재의 3요소를 평가
(라) 금속의 점화 메커니즘에는 입자충격, 마찰가열/용착, 전기아크, 비금속/오염물질로 인한 점화 촉진등의 변수 포함
(마) 비금속의 점화 메커니즘에는 압축가열, 기계적충격, 유동마찰, 정전기 방전 등의 변수가 포함.
(바) 작업자 및 운전에 영향을 주는 심각도를 기준으로 화재의 결과를 평가
(사) 부품목록, 사용하는 재질, 도면, 절차등을 평가
(아) 필요한 경우 화재 가능성을 낮추고, 가능하면 화재의 피해를 낮추기 위해 권장사항을 작성
(자) 화재 위험이나 화재의 피해를 줄이기 위해 다음 순서로 검토한다.
① 재질변경
② 설계변경
③ 작업방법변경
④ 격리, 방호구획 설정, 방호장치 설치, 보호구착용 등
4.3 금속재질선정
4.3.1 일반사항
(1) 재질선정에서 가장 중요한것은 최악의 운전조건에서 재질이 타지않는 재질을 선정하는 것이다.
(2) 금속의가연성에주요한영향을미치는주요 변수는합금화학, 재질두께,운전온도및산소압력과순도등이있다.
(3) 산소배관에서 사용하는 재질은 부록1의 면제재질을 <그림1> 충돌 속도곡선 및 <그림2> 비충돌 속도 곡선을 이용하여 이송속도를 선정할 수 있다.
(4) 여기에 나열된 많은 합금의 면제압력은 ASTM G124 및 기타 설계요소의 가연성 자료를 기준으로 한다.
(5) 입자충돌에 의한 점화 위험을 최소화하기 위해 주어진 최소두께에 대해 면제 압력보다 큰 압력에서 선택된 합금이 사용 가능한 가스 속도이다.
(6) 사용압력이 주어진 최소 두께에 대해 공표된 면제압력보다 큰 경우, 적용되는 가스의 속도는 충돌부위의 존재에따라 특정 압력속도 곡선 아래영역을 준수하여야 한다.
(7) 운전압력이면 제압력보다 작을 경우, 합금은 내화성으로 간주되므로 속도에 제한이 필요하지 않다.
(8) 압력속도 곡선은 입자충돌 점화 메커니즘만을 다룬다는 것을 이해해야 한다.
(9) 다른점화 메커니즘이 있다면, 관련근거에 따라 위험성평가를 하여야 한다.
(10) 알루미늄 합금은 콜드박스 외부의 가스 산소배관서리에 사용해서는 안된다.
(11) 앞의 4.2 (3) 에서 설명에 따라 산소 위험분석을 수행하여 사용할 수 있는 다른 선택을 할 수 있는 간단한 방법이다.
4.3.2 표준순도 산소에 대한 면제압력
(1) 부록1은 면제압력이 확인된 합금 성분의 화학적 조성을 %로 표시하고 있다.
(2) 부록 1에 열거되지 않은 합금에 대해서는 가연성 평가를 실시하여야 한다.
(3) 부록 2는 면제압력이확인된금속에대한면제압력목록으로두께가30㎜미만의연소기준에기초한것이다.
(4) 두께는 합금성분과 함께 중요한 변수로 합금의 최소두께는 부록2 에 규정된 최소두께 이상이어야 한다. 만약 최소두께보다작으면가연성으로간주해야하고, 배관압력에적합한속도제한을준수해야한다.
(5) 면제압력은 3.2∼6.4㎜의 주어진 두께범위를 벗어나면 안된다.
(6) 4.2 (1)항에 기술된 적절한 특성화 기법을 사용하여 가연성 평가를 수행할 수 있으며, 이때 속도를 제한할 필요는 없다.
(7) 압력속도값이 <그림1>과 <그림2>의 곡선보다 낮거나 위험평가에서 발화가 발생할 가능성이 없거나 다른 안전조치에 의해 완화될 수 있는 경우 재질은 면제 압력이상으로 사용할 수 있다.
(8) 보호 라이너 및 용접 오버레이(Protective liners and weld overlays) 또는내화 합금의 코팅은 높은 산소속도와 압력이 입자 충돌 점화 시나리오를 초래할 수 있는 탄소강 또는 스테인리스 강 화학성분과 함께 사용할 수 있다.
(9) 일반적으로 구리, 니켈 또는 모넬합금을 사용한다.
(10) 최소두께는 재질선택, 시험 데이터, 운전조건, 경험등의 기준에 따라 선정한다.
(11) 일반적으로 용접 오버레이, 코팅 또는 라이너 두께는 일반적으로1∼3㎜를 사용한다. 하지만 전기 도금된 표면은 수소 흡수, 박막보호 코팅의 마모 침식 등과 같은 요소를 평가하는 특정 위험성평가를 수행되지 않는 한 부적합한두께로인해권장되지않는다.
(12) 내마모성이 필요한 경우 경질합금도 가능성이 있다. 그러나 경질합금과 그 모재합금 내화성은 배관설비 내 부속도, 부록2에 표시된 면제 압력 또는 자세한 위험성평가를 기반으로 하는 공정조건에 대해 만족해야 한다.
(13) 압력속도곡선은입자충돌점화 메커니즘만적용하기때문에액체산소를기화시켜제조된기체산소는충돌을일으킬수 있는입자를적절하게세척, 방출(Blowout)하여야하며, 검사및시운전이나사용기간동안에이물질의입자가생성되지않는위험성평가를실시하고, 이물질생성을최소화할수 있는스테인레스 재질을선정할수 있다.
4.3.3 저순도산소
(1) 산소압력 및 온도와 같은 특정 파라미터에 따라 산소순도가 감소하면 점화 이벤트가 발생할 경우 금속 가연성이저하될 수 있습니다. 따라서 속도제한을 적용하지 않을 수 있다.
(2) 세가지 옵션을 다음과 같이 고려할 수 있습니다.
(가) 옵션1. 표준순도 산소 농도 이하의 가스 산소는 99.5% 이상의 표준 순도 산소농도와 동일하게 처리하고, 표준순도산소에 대해 부록 2 에 나열된 면제 압력을 사용한다. 이것은 산소순도가 감소함에 따라 점점 더보수적이고 매우 안전한 접근법이다.
(나) 옵션2. 감소된 순도 산소는 가스 혼합물의 산소부분 압력과 동일한 압력에서 순수 산소가스와 동등한것으로 처리한다. 따라서 순도감소특정산소 가스 혼합물에 대해 부록 D에 나열된 면제압력은 산소부분 압력을 나타낸다. 이것은 안전하지만 옵션1만큼 보수적이지 않다.
(다) 옵션3. 인화성 시험은 4.2 (1) 및 부록1에 기술된 절차를 사용하여 순도가 낮은 산소환경에서 적합한 재질을 사용하여 수행할 수 있다. 소재가 내화성이 없는경우 다음4.4에 표시된 산소속도 제한을 해야 한다. 테스트 결과 금속이 두께, 산소순도 및 관심 압력에 대해 내화성이 있는것으로 나타날 경우 속도제한을 가할 필요가 없다.
(3) 최대 21MPa의 압력과 부피기준으로 산소 함량이 35% 미만일때, 탄화수소가 없고 철 및/또는 비철재질로 구성된 배관설비는 속도제한에서 제외될 수 있다. 이러한 조건에서 탄소강과 스테인리스강은 모두 추진 점화 연소시험방법에 의해 내화성 물질임이 입증되었다(부록1참조). 단, 이러한 배관재질은 산소 서비스 세척 및 4.5에 설명된 것과 같이 산소와 호환되지 않는 비금속 사용이 권장된다.
4.3.4 초고순도산소(UHP, Ultra high purity oxygen)
(1) 초고순도 산소는 반도체와 전자제품과 같은 첨단기술에 점점 더 많이 이용되고 있다. 이러한 응용분야의 특수요건은 산소를 오염시킬 수 있고, 입자충돌 점화 메커니즘에 기여할 수 있는 미입자 제거를 요구한다. 초고순도 산소 설비는 특수 세척절차 외에도 미립자가 없는 상태를 보장하기 위해 특수 모니터링 절차를 한 경우에는 일반적으로스테인리스강을 사용할 수 있다.
(2) 초고순도 산소 스테인리스 배관 세척은 초고순도 산소 설비에 미립자와 점화 가능한 오염물이 없는것은 입자 충격 메커니즘에서 발화를 방지하는 가장 중요한 요인이다. 따라서 비금속성 구성품을 점화시킬 수 있는 다른점화 메커니즘(예:단열압축)이 존재할 수 있지만 세척이 잘되고 적절히 유지되는 초고순도 산소설비는 산소속도 요건에서 면제된다.
(3) 초고순도 산소 배관설비의 세척은 1,000µg/m³ NVR(Non-volatile residue)을 초과하지 않는 오염물질 수준을 충족할 수 있는 자격을 가진 특수 청소전문업체가 실시하여야 한다.
4.3.5 온도제한
(1) 4.2에서 금속 가연성 및 점화성 정보는 최대 200℃의 가스 산소배관 및 배관설비와 관련이 있다.
(2) (1)항의 제약조건을 초과하는 온도에서 작동하는 배관설비는 안전을 보장하기 위해 높은 온도에서 추가 분석 및/또는 시험을 필요로 한다.
(3) 운전온도가 –20℃ 미만인 경우, 철강은 다른 산업용 가스와 동일한 방법으로 적절한 연성 및 파괴 인성값을 입증하여야 한다.
(4) 고온의 산소설비는 주위의 건축용 일반철강에서 녹이유입되어 설비 내에서 스폴링(spallings, 부스러짐)이나 입자 생성등의 기계적 성질이 변경될 위험이 있어 재질 선정에 주의하여야 한다.
4.4 유속과 가스 압력
4.4.1 일반사항
(1) 배관의직경은주로설계속도에기반으로한다. 이속도는정상적인공정의운전과환기를기반으로하며, 기계적고장또는제어밸브고장또는릴리프밸브리프팅과같은기타비정상적인상황으로인해발생할수 있는속도를기반으로하지않는다.
(2) 속도는 정의된 모든 작동압력, 온도 및 유량에서 파이프 내의 평균속도를 말한다.
(3) 배관의 속도는 구성 요소의 최소 단면적 유량영역에 기초해야 한다.
4.4.2 배관 및 장비에 대한 충격속도 곡선 및 재질선정
(1) <그림2>와 같은 충돌속도 곡선을 이용하여 새로운 배관, 밸브, 장비 및 관련 배관설비의 설계 및 재질선정을 하여야 한다. 자세한 사항은 5.2.1 및 5.2.2를 참조한다.
(2) 설계자는 3.2.7에서 정의된 충돌속도 곡선 및 면제압력에 따라 재질을 선택할 수 있다. 면제압력(부록2 참조)보다 작은 금속은 속도제한없이 사용할 수 있다.
(3) 면제압력보다 큰 경우 설계자는 속도가충돌속도곡선아래로유지되는지확인하여야한다.
(4) 충돌속도 곡선미만의 속도에는 탄소강, 스테인리스강 및 기타 면제재질을 사용할 수 있다.
(5) 충돌속도 곡선 위에서는 면제 재질을 사용하거나 위험을 완화하기 위한 적절한 조치를 하여야한다.
(6) 배관 및 배관 설비는 일반적으로 탄소강으로 제작되기 때문에 가스속도를 충돌속도 곡선 아래의 값으로 제한하여야 한다.
(7) 다른 설계 고려사항은 압력강하, 기체완충효과, 소음감소, 진동 및 운동에너지를 제한할 필요가 있는 낮은속도 등이 있다.
(8) 비충돌 설비의 속도제한은 4.4.3을 참조한다.
(9) 0.21MPa(30psi) 미만 압력의 경우 업계 관행적으로 적절한 위험평가와 함께 적절히 설계된 구성요소를 사용하여 속도 제한없이 산소 서비스에 탄소강과 얇은 두께의 스테인리스강을 사용하고 있다.
(10) 이는 저압 가연성 테스트에서 이러한 물질에 의해 나타난 낮은 연소율 때문이다. 하지만 이러한 경우 적용하는구성요소는 사례별로 위험성평가를 실시하는것을 권장한다.
(11) 다음의 경우에는 배관설비의 위험성평가에서 내화성 재질의 사용 대신에 다른 재질을 사용할 수 있다.
(가) 충돌위치에서 면제 재질로 만든 보호판을 사용
(나) 150㎛ 이하의 입자를 제거할 수 있는 여과장치를 사용하여 충돌입자를 최소화
(다) 단4.2.3, 4.2.4, 5.2.2 및 5.2.3에 나열된 사항은 제외
(12) <그림2>에 표시된 곡선은 최대 200℃의 설계온도에 유효하다.
(13) <그림2>의 충돌속도 곡선의 방정식은 다음과 같이 정의된다.
(가) 0.3MPa, abs < P< 1.5MPa), abs이면, V(m/s)= 30m/s
(나) 1.5MPa, abs <P<10MPa, abs이면, P·V= 45MPa, abs·m/s
(다) 1MPa, abs < P< 20MPa, abs이면, V(m/s)= 4.5m/s

<그림 1> 충돌 속도 곡선
4.4.3 비충돌설비의 속도제한
(1) 속도는 배관설비의 비충돌 설비의 비충돌 부위에서 <그림2> 비충돌 속도곡선에 나타낸 곡선까지 사용할 수 있다. 기타 자세한 내용은 5.2.1, 5.2.2를 참조 한다.
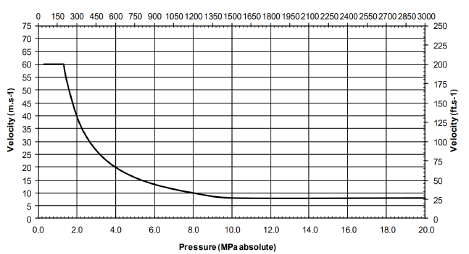
<그림2> 비충돌 속도 곡선
(2) 비충돌 속도 곡선보다 큰 속도의 경우 면제재질을 사용하거나, 위험을 완화하기 위해 대체조치를하여야한다.
(3)<그림3>에표시된곡선은최대200°C의온도와 압력은최대21MPa로제한된다.
(4) 비충돌속도곡선의방정식은다음과같이정의된다.
가) 만약 0.3MPa, abs< P< 1.5MPa, abs일 경우 V(m/s)= 60m/s
나) 만약 1.5MPa, abs< P<10MPa, abs일 경우 P·V= 80MPa, abs·m/s
다) 만약 10MPa, abs< P< 20MPa, abs일 경우 V(m/s)= 8m/s
4.5 비금속 재질 선정
4.5.1 비금속 재질의 특성 및 위험성
(1) 대부분의 비금속은 금속보다 산소와 반응이 잘 일어나지 않는다.
(2) 비금속은 마찰을 줄이고, 가스 누출을 최소화하기 위해 주로 개스킷, 밸브시트, 나사산 윤활제, 나사산씰, 밸브패킹 및 유사한 용도에 사용된다.
(3) 압력이 낮고, 순도가 23.5% 보다 높은 경우에도 많은 비금속은 산소에서 가연성이 있다.
(4) 점화 및 화재 확산에 영향을 미치는 주요요인은 압력, 온도 및 산소농도이다.
(5) 오염된 비금속 재질은 점화에 영향을 줄 수 있다.
(6) 산소지수(OI)는 테스트 샘플을 연소시킬 수 있는 산소-질소가스 혼합물의 최소 산소 농도로 산소 지수가 높은것을 사용하는것이 좋다.
(7) 일반적으로 비금속 재질의 산소지수는 압력이 증가할수록 감소한다.
(8) 비금속 재질은 금속재질의 가연물로 작용하는 촉진제로 사용되는 경우도 있다. 따라서 비금속 재질의 연소열은중요한 매개변수가 될 수 있어 연소열은 2,500cal/g 미만이이어야 한다.
(9) 비금속 재질과 산소와 반응을 평가하기 위해 고려해야 하는 중요한 변수는 자동점화온도(AIT) 이다.
(10) 비금속 재질의 점화는 사용하는 설비나 공정(예 : 가스화 공정, 열교환기 등)에 따라 특정 운전조건 또는 특정 장비 내에서 마찰에 의한 가열 등으로 자동점화온도를 초과할 수 있다.
(11) 실제로 최소 자동점화온도는 ASTM G72에서 규정한 절차에 따라 최소시험압력103 bar, abs, 최소 300°C에서 시험하고, 운전온도와 자동점화온도(AIT)는 100℃ 이상 여유를 주는것이 일반적이지만, 50℃ 이하의 여유를 줄경우에는 별도의 평가를 실시하여야 한다.
(12) 비금속 재질은 서서히 산화되고, 노화되면서 재질의 특성이 변화(화재발생)될 수 있다. 특히 예비품을 선정할때 산소와 반응성 여부, 즉 화재발생 여부를 확인하는 것은 필수적이다.
(13) 비금속 재질의 점화 에너지는 다음과 같다.
(가) 산소의 단열압축
(나) 진동, 공진 또는 흐름 마찰로 인한 연성소재 자체의 내부변형
(다) 변형후 기계적 충돌, 마찰 또는파열
(라) 정전기 방전 불꽃
(마) 점화촉진(입자 또는 기타 에너지원 연소등)
(14) 점화 확률평가와 반응 효과 평가가 결합되면 설계자는 재질의 설계와 선택을 최적화할 수 있다. 이 절차의 예는ASTM G63을 참조한다.
4.5.2 설계관행 및 재질 선택
(1) 비금속이 포함된 배관설비를 설계할 때는 다음 관행을 따르는것이 바람직하다.
(가) 산소설비 사용되는 비금속양을 최소화한다.
(나) 연소열이 낮고 자동점화온도(AIT)가 높은 비금속 재질을 선정한다.(4.5.1참조)
(다) 방열판 역할을 할 수 있는 높은 열전도성을 가진 적절한 질량의 내화성 금속에 비금속 부품을 내장하여 설계시 열분산을 고려한다.
(라) 비금속은 유제 흐름에 직접 접촉되지 않도록 한다.
(마) 구성부품의 과도한 움직임을 방지 한다.
(바) 운전조건에서 비금속 재질의 물리적, 화학적 안정성이 확보되어야 한다.
(사) 비금속 부품들은 절연 접합부를 제외한 내부 부품간의 전기적 연속성을 유지하여야 한다.
(2) 이러한 설계방법외에도 특수 세척용제를 사용하는 경우 세척절차와 방법에 특별히 주의해야 한다.특히 세척용제와 비금속 재질이 반응하거나, 용해시키는지를 점검하여 오염된 용제에 의해 비금속 부품 또는 장비품목이 오염되지 않도록 하는것이 중요하다. 모든 잔류물질은 반드시 제거하여야 한다.
(3) 비금속 재질을 사용하는 부품을 설계, 설치하는구체적인정보는해당표준을참조한다.
(4) 특히 산소 감압기와 같이 단열 압축에 노출된 부품들과 작은 부품들은 시험절차가 적절한지를 확인하여야 한다.
(5) 산소설비에 사용할 수 있는 비금속 재질은 다음을 참조하여 제조자와 사용가능한 온도, 압력 및 산소의 순도 등을 협의하여 결정하여야 한다.
(가) 불소수지(Fluorinated polymers : Polytetrafluoroethylene(PTFE), 불소에틸렌프로필렌수지(Fluorinated ethylene-propylene(FEP), polychlorotrifluoroethylene(PCTFE)
(나) Fluoroelastomers
(다) Amorphouspolymers: Polyimides
(라) 완전히 산화된 세라믹과 유리는 불에 잘 타지 않지만 부서지기 쉬워 일반적으로 복합 제품으로 바인더와 함께사용
(마) 경고1 : 불소 폴리머는 연소시 유독가스를 방출할 수 있다.
(바) 경고2 : 비금속 부품은 변경될 수 있어 사용자는 산소설비에 사용하기전에 반드시 비금속재질이 적합한지를 확인하여야 한다.
4.6 배관 및 배관설비
4.6.1 지하배관
(1) 지하배관은 KOSHA GUIDE P – 158 - 2017“장거리 이송배관 안전관리에 관한 기술지침”, API1104“Welding of Pipelines and Related Facilities” 또는기타 공인코드와 같은 사양 및 검사코드에 따라 용접 시공되어야 한다.
(2) 지하배관은 부식 방지를 위해 관련법률에 따라 외부코팅을 하여야 한다.
(3) 지하 산소배관 및 배관은 특히 배관재질에 점화될 수 있는 낙뢰 또는 접지 고장조건에 의한 손상에 취약하다.
(4) 음극방식 문제를 방지하기 위해 지하 산소배관과 지상배관 또는기타 금속구조물 사이는 KOSHA GUIDE D – 51- 2020,“지하 -지상배관 연결부의 절연 플랜지 설치에 관한 기술지침”에 따라 전기적 연속성을 피해야 한다.
(5) 누출 가능성이 높은 플랜지 연결부위는 지하에 매립하거나, 피트에 설치하지 않는것을 권장한다.
4.6.2 지상배관
(1) 지상 산소배관 및 설비는 다른 지상 배관설비에 적용되는 적절한 기계적 설계 관행을 따라야한다.
(2) 지상 탄소강 배관 및 배관설비는 대기부식을 방지하기 위해 도장하여야 한다.
(3) 지상 배관설비의 지상부분은 음극방식설비를 격리하기 위해 KOSHA GUIDE D – 51- 2020,“지하-지상 배관연결부의 절연 플랜지 설치에 관한 기술지침” 전기 절연 접합부를 통해 매립부분에 연결되어야 한다.
(4) 모든 지상 배관 및 배관설비는 절연조인트를 제외하고 모든 연결부에 걸쳐 전기 통전성을 가져야하며, 번개와 정전기의 영향을 방지하기 위해 적절한 간격으로 접지되어야한다.
(5) 낙뢰보호를위해설치된지상배관및배관설비의접지측 전기저항이10Ω이하이어야한다.
(6) 플랜지연결부위는KOSHAGUIDEE–38–2012,“접지선과접속방법에관한기술지침”에따라등전위접지를하여야한다. 하지만플랜지볼트는볼트가전기재질또는페인트로코팅되어있지않고녹을방지하기위해잘유지되는경우 접지를생략할수 있다.
(7) 절연플랜지를사용하지않는지상배관이짧은경우, 배관은절연패드등을사용하여지지구조물로부터절연되어야한다.
(8) 산소배관은산소와 접촉하여위험상황을초래할우려가있는위험물질을이송하는배관과안전거리를유지하여야한다.
(9) 다중배관이 지나는 파이프랙에 산소배관을 설치하는 경우, 가능한 이격거리를 멀리하고, 산소배관의 기계적 연결 부위에서 동시에 누출 또는 고장이 발생할 수 있는 경우를 대비하여 위험한 혼합물이 발생할 수 있는 다른 유체 배관의 기계적 연결부와 근처에 배치하는것을 금지한다.
(10) 산소 배관의 기계적 연결 부위 근처의 다른배관은 화재로부터 보호하여야 한다.
(11) 산소배관은 고온 가스 또는 증기 통풍구의 외부 충돌, 외부 진동체, 배관 위로 오일 누출 등의 고장이나, 위험한상황을 초래할 수 있는 외부힘에 불필요하게 노출되어서는 안된다.
4.6.3 배관표시 등
(1) 지상배관은 KOSHA GUIDE G - 4 – 2011,“배관 내 이송물질 표시에 관한 안전 가이드”를 참조하여 관련법규, 규정 또는 기업표준에 따라 색상 코드 및/또는 식별되어야 한다.
(2) 지하배관은 매설된 배관의 수직 상부 지상근처에 표지로 확인될 수 있도록해야하며 표지는 배관의 경로를 나타낼 수 있도록 일정한 간격과 방향이 변경되는곳에 설치해야 한다.
(3) 배관 외부와 토양사이에 발생하는 갈바닉현상에 의한 부식은 기계적 손상을 제외하고, 가장 빈번하게 배관에서누출을 발생시키는 원인이 될 수 있다.
(4) 지하 이송 배관은 부식을 방지하기 위해서는 KOSHA GUIDE M – 116 – 2012,“기기 및 배관의 부식 관리 기술지침” 등에 따라 부식 관리를 하여야 한다.
(5) 지상배관 및 지하배관은 관련법 등에서 규정한 사항은 준수하여야 한다.
5. 배관, 밸브 및 부속설비등
5.1 일반사항
이 절은 제4절에 제시된 설계원칙을 배관, 밸브 및 부속설비(이하 배관이라 한다.)에 실제로 적용할 수 있는 방법을설명한다.
5.5.1 재질선정기준
(1) 배관, 밸브 및 장비에 대한 재질 선택은 4.1, 4.2, 4.3 및 4.4에 기초해야 한다.
(2) 이물질등에 의한 충돌이 일어날 수 있는 배관에서 재질선정은 4.4.2에서 설명한 <그림2> 의 충돌속도 곡선에 기초해야 한다.
(3) 충돌이 일어날 수 없는 배관에서 재질선정은 탄소강과 스테인리스강의 속도는 증가할 수 있지만 <그림2> 비충돌속도곡선에 의해 제한되어야 한다.
(4) 다음은 5.2에서 5.5까지 충돌이 일어날 수 있는 배관이나 충돌이 일어나 수 없는 배관설비의 구체적인 배관재질선정방법을 제시한다.
5.2 배관 및 부속품
5.2.1 충돌이 일어날 수 있는 배관
(1) 유체흐름이 갑자기 방향을 바꾸거나, 소용돌이가 있으면 배관 벽면에 입자가 벽에 충돌할 때 일어난다.
(2) 충돌이 일어날 수 있는 곳은 다음과 같지만 이에 국한되지 않는다.
(가) 맞대기 용접과 소켓용접티와 소켓용접엘보우(Elbow)
(나) 분기관, Weldolets, sockolets, andthreadolets등으로 연결관 분기관
(다) 다공성 산소환산기(Multi-holediffuser) 및 그 와 관련된설비
(라) 곡률 반경이 짧은 엘보우(Elbow)s (Radius of curvature less than 1.5 diameter)
(마) Socket-weld and threaded reducers
(바) 확관비가 3: 1 이상이면서 좁아지는 Eccentric and concentric reducers
(사) 20° 이상 굴곡진 새우등 곡관(Mitred elbows)
(아) 감압밸브의 출구에서 직경의 8배까지
(자) 기타밸브는 5.3, 스트레이너 등은 5.4를 참조
5.2.2 충돌이 일어나지 않는 배관
(1) 충돌이 일어날 수 없는 곳은 다음과 같지만이에 국한되지 않는다.
(가) 직선 배관
(나) 곡률반경이 큰 맞대기 용접티(Tee)
(다) 곡률 반경이 큰 엘보우(Elbow)(직경의1.5배이상인반경)
(라) 내부표면이 매끄러운 6개 이상의 단관(5개소 이상 용접)으로 제작된 90° 새우등 곡관
(마) 내부표면이 매끄러운 3개 이상의 단관(2개소 이상 용접)으로 제작된45° 새우등 곡관
(바) 최대 3: 1로 감소하는 reducers
5.2.3 특정배관위치
(1) 우회 배관(Bypass piping)
(가) 우회밸브의 입구와 출구 <그림3> 배관재질은 가압할때 빠른유속과 난류흐름에 노출되기 때문에 특별히 고려되어야 한다.
(나) 우회 배관의 앞쪽은 충돌이 일어날 수 없는 배관으로 간주한다. 하지만 양방향으로 흐르는 경우에는 충돌이 일어날 수 있는 배관으로 간주되어야 한다.
(다) 따라서 양방향 흐름이 가능한 경우 우회밸브의 하류 및 전체 우회 배관에 대해 면제재질이 권장된다.
(2) 배관방출(Piping upstream of vents and bleeds)
(가) 방출 및 블리딩 밸브(bleeding valve)의 업스트림 지점배관과 모든 배관설비의 블리딩 밸브(bleeding valve)(즉, 격리 밸브사이)는 우회 배관으로 설계되어야 한다.
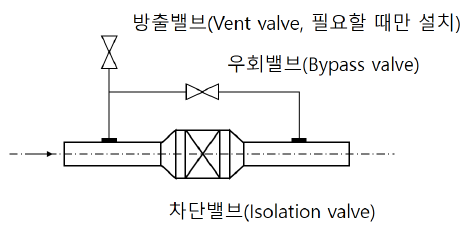
<그림3> 우회 배관설치 사례
(3) 안전밸브 입구배관
(가) 안전밸브 입구배관 재질선정은 안전밸브 설정압력에서 최대유량을 적용한다.
(4) 대기 방출밸브와 안전밸브의 방출배관
(가) 방출 배관의 재질선정은 충돌속도곡선에 기초해야 한다.
(나) 방출 배관은 대기중에 노출되고, 일교차에 의한 결로가 일어나기 때문에 일반적으로 내식성 재질을 사용한다.
(다) 대기로 방출하는 배관은 방출배관의 출구에서 난류가 일어나지 않도록 제어된 단면 탄소강을 사용할 수 있다. 그러나 면제재질은 모두 내식성과 내연성이 있어야 한다.
(라) 안전밸브의 방출구는 옥외 안전한곳에 위치하여야 한다.
(마) 방출구 주위의 산소농도가 높아 위험을 최소화하기 위해 환기구의 위치, 높이, 방향, 적절한 간격등을 고려해야한다.
(5) 감압되는 설비의 배관(Piping downstream of pressure letdown sites)
(가) 감압조절 수동밸브, 공정제어밸브(5.3.2(3)항 참조) 또는 제한 오리피스와 같은 감압장치의 출구배관은 유속이빠르고, 높은 난류가 흐른다.
(나) 출구배관의 벽은 배관 직경의 8배가 되는곳까지를 충돌이 일어날 수 있는것을 고려하여 면제재질로 설치하여야 한다.
(다) 하지만 입자 충돌 또 충돌에너지를 다음과 같이 줄일 수 있다면 면제재질을 사용하지 않을 수 있다.
① 만약 150㎛이하의 체(스크린, screen)를 감압설비 전단에 설치하여 충돌가능성을 현저하게 감소시킬 수 있는 경우
② 다공성 산소환산기(Multi-holediffuser)에서 압력강하가 발생하는 경우 환산기 출구는 고속난류제트가 없는것으로 간주할 수 있다.
③ 작업자가 접근할 수 없도록하거나, 노출되지 않도록 차폐가 된 경우
(6) 개스킷
(가) 개스킷과 배관의 내경이 일치하도록하여 입자가 충돌할 수 있는 공간을 최소화 해야한다.
(나) 가스킷 내경은 배관의 반경과 같고, 돌출되지 않도록 설치하여야 한다.
(다) 산소배관에 사용하는가스켓은 깨끗하게 제조되어야 하고, 탄화수소계 접착제,윤활제등을 사용할 수 없다.
(라) 산소와 반응할 수 있는 탄화수소등의 물질로 세척하면 개스킷에 세척액이 침투될 수 있어 사용할 수 없다.
(마) 산소 사용자는 나사산 실란트 재질이 최대 서비스 압력 및 온도에서 산소공급과 호환되는지 확인해야한다.
(바) 나선형 개스킷(Spiralwound gaskets)은 권선이 변형되지않도록 배관의 내경과 같은 내부링(Inner rings)이있어야 한다.
(사) 개스킷 실란트(Gasket sealant)는 유체가 흐를때 난류가 발생할 수 있어 권장되지 않지만, 실란트가 필요한 경우에는 4.5의 규정을 만족시켜야한다.
(아) 기타 자세한 사항은 ASTM G63은 비금속선택에 대한 지침을 참조한다.
(7) 나사산 실란트(Thread sealants)
(가) 나사산 실란트 재질이 최대 서비스 압력 및 온도에서 산소공급과 호환되는지 확인해야 한다.
(나) PTFE 테이프는 산소취급 설비와 호환성을 보장하기 위해 청결도를 포함한 사양에 따라 사용할 수 있다(4.5참조).
(다) 연결부밖으로 돌출되지 않도록 최소량의 나사산 실란트를 도포하여야 한다.
(라) 나사산 실란트의 개방된 용기의 오염을 방지하기 위한 규정이 마련되어야 한다.
(마) 기타 자세한사항은 ASTM G63은 비금속선택에 대한 지침을 참조한다.
(8) 먼지트랩(Dust traps) and 관 말단(Dead ends)
(가) 쇳가루(Bulk metal)의 발화 위험은 입자 질량에 따라 증가함으로 먼지트랩이나 정체공간은 쇳가루입자가 쌓이지 않도록하는것이 중요하다.
(나) 모든 배관설비에서 쇳가루입자가 축적될 수 있는 정체공간이 있는지를 확인하고, 설계 및 안전운전절차를 작성하여 지속적으로 관리하여야 한다.
(다) 특히, 연결부가 주배관의 상단 또는 최소한 수평으로 동일한 레벨에 있어야하는 우회 배관, 방출구 또는 퍼지라인과 같은 예비설비의 배관을 포함하여 정체구간에 입자가 쌓이지 않도록 관리하여야 한다.
(라) 먼지트랩(Dust traps)과 정체구간은 설치하거나 형성되지 않도록 하여야 한다.
(마) 먼지트랩(Dust traps)을 예를 들면 매니폴드, 확대된 직경티, 개스킷 등은 플랜지 내경을 따라 세척되지 않을 수 있고, 주배관 아래쪽으로 설치한 예비 배관설비 및 기타 유속이 감소하는 구간에서는 입자가 떨어져 쌓일 수 있다.
(9) Fire stops
(가) Fire stops은 구리 또는 니켈 합금으로 만든 짧은강관으로 제작된 배관이송설비나 분기관에 설치하여야 한다.
5.3 밸브기능 및 특징
5.3.1 일반사항
(1) 산소설비에 사용이 가능한 밸브는 관련법규나 규정에 적합한 자격을 갖춘 공급업체로부터 조달되어야 한다.
(2) 재질이나 기능은 정상 또는 비정상 운전조건에서도 원활하게 작동될 수 있는것으로 설치하여야 한다.
(3) 재질선정요건은 밸브고유의 설계, 기능 및 형식에 따라 유속, 잠재적인 충돌면과 관련이있다.
5.3.2 밸브기능
(1) 다음과 같은 밸브의 기능에 대해서 규정한다.
(가) 차단밸브(Isolation valves)
(나) 조절밸브 및 공정제어밸브(Throttling or process control valves)
(다) 긴급차단밸브(Emergency shutoff valves)
(라) 우회밸브(Bypass valves)
(마) 방출밸브(Vent valves)
(바) 안전밸브(Pressure relief valves)
(사) 역지밸브(Check valves)
(2) 차단밸브 위험성(Isolation valve risks)
(가) 시트 전체에 걸쳐 차압으로 개방되는 격리밸브에는 두가지 위험요인이 있다.
① 개방중밸브를 통과하는 고속 및 난류
② 단열압축으로 인한 급격한 다운스트림의 압력 및 온도상승
(나) 빠른유속, 난류 및 급속 가압 위험은 개방되기 전에 격리밸브의 압력을 균일하게 할 수 있는 우회 배관을 사용하면 방지할 수 있다.
(다) 우회밸브는 다음(6)에 설명되어 있다.
(라) 차단밸브는 일반적으로 게이트, 볼, 플러그 또는 나비형 등이 있다.
(마) 차단밸브는 완전히 닫히거나 완전히 개방된 위치에서 작동해야하며 조절모드에서 작동하면 안된다.
(바) 이들장치는 우회 배관 또는특정작동절차를 사용하여 현저한 압력차이 없이 작동해야 한다.
(사) 차단밸브 이후의 가압속도는 단열압축의 위험을 방지하기 위해 제어 되어야 한다.
(아) 열거나 닫거나하여 차압으로 작동하는 밸브는 조절밸브 또는 공정제어 밸브로 간주하여 다음(4)를 참조한다.
(자) 높은압력으로 운전하는 차단밸브에서 누출될경우 누출속도가 아주빠르다는 것을 의미한다.
(3) 조절밸브 또는 공정제어밸브(Throttling or process control valves)
(가) 조절 또는 공정제어밸브는 유량 또는 압력을 제어하는 밸브로 압력제어, 유량제어, 바이패스 또는 안전밸브가 포함된다.
(나) 필요한 기능에 따라 압력조절밸브는 지속적으로 흐름을 조절하거나, 천천히 열리거나 닫히거나, 빠르게 열리거나 닫히도록 프로그래밍할 수 있다.
(다) 대부분의 경우 공정제어밸브는 자동화되지만, 여기서는 수동조작 스로틀 밸브 및 스프링 작동조절기를 포함한다.
(라) 고정제어밸브는 산소설비에서 가장 엄격한 서비스 등급에 해당된다.
(마) 이는 그 기능이 유량을 조절하거나 고속 및 난류 충돌흐름과 관련된 높은 압력차이로 작동하기 때문이다.
(바) 난류 및 충돌은 밸브의 트림과 본체에만 존재할 뿐아니라 최소한 배관 직경의 8배이상의 하류배관까지 영향을주는것으로 간주해야 한다. 또한 양방향 유량이 흐른다면 상류/하류 배관에 난류 및 충돌이 일어날 수 있다.
(사) 고정제어밸브는 일반적으로 글로브, 변형된 볼, 편심 플러그 또는 버터플라이 등의 유형이 있다. 차단밸브의 정의를 충족하지 않는 밸브는 조절밸브로 간주해야 한다.
(4) 긴급차단밸브(Emergency shut-off valves)
(가) 비상차단밸브는 일반적으로 자동화되고, 완전히 개방된 위치에서 작동하다가 비상상황이 발생한경우에만닫힌다.
(나) 비상차단밸브는 높은 유량밸브이며, 일반적으로 게이트, 나이프게이트, 버터플라이 또는 볼타입 등이 있다.
(다) 정상작동시 밸브는 비충돌 유량을 경험하지만, 닫힐때 빠른 유속과 순간적인 난류가 발생할 수 있어 비상차단밸브는 조절밸브로 간주한다.
(5) 우회밸브(Bypassvalves)
(가) 우회밸브는 일반적으로 수동차단밸브를 조작하여 업스트림에서 바로 다운스트림으로 배관을 연결한다.
(나) 공정설계에 따라 우회밸브는 특정공정제어 또는 비상차단밸브에 우회 배관이 필요할 수 있다.
(다) 차단밸브의 전후 압력을 동일하게하여 차단밸브를 안전하게 열 수 있도록 우회밸브를 설치한다. 또한 우회밸브는 과도한 속도와 빠른가압의 위험을 완화하기 위해 다운스트림 배관설비를 천천히 가압하는데도 사용된다.
(라) 제어되고 느린가압을 위하여 스로틀 흐름 제어식 밸브를 사용해야 한다.
(마)우회밸브는 흐름제어기능으로 인해 스로틀 또는고정제어밸브로 분류되지만 일반적으로 수동으로 작동하는 밸브이다.
(바) 일반적으로 밸브 본체 전체에 걸쳐 충돌과 고속의 난류가 흐르는 글로브 밸브를 사용한다.
(사) 우회밸브는 유체가 양방향으로 흐르거나, 위험성 분석 결과 우회 배관으로 판정되면 밸브와 주위배관은 면제재질을 권장한다.
(아) 액체산소를 기화시켜 기체 산소를 생산하는 설비는 4.3.1을 참조한다.
(자) 우회밸브는 다음기준에 따라 설계·설치·운전되어야 한다.
① 허용시간내에 균일한 압력으로 달성할 수 있는 크기
② 우회 배관에 이물질이 쌓이는것을 최소화시킬 수 있도록 <그림3>을 참조하여 주관의 상부에 설치하여야 한다.
(차) 우회 배관은 주배관의 연결부위가 돌출되지 않도록 설치하여 유체에 포함된이 물질과 충돌하는것을 방지하여야 한다.
(6) 방출밸브(Vent valves)
(가) 방출밸브는 빠른유속과 이물질의 충돌이 발생하여 조절밸브로 간주한다.
(나) 방출밸브의 재질선정은 5.2.3 (2)와 (4)를 참조한다.
5.3.3 밸브 특징
(1) 밸브를 통과하는 유속은 글로브밸브나 감압밸브의 경우 유체가 흐르는 단면적의 변화에 따라 달라진다.
(2) 정상적으로 완전히 개방되는 볼, 플러그, 나비 및 게이트 타입과 같은 차단밸브의 경우, 속도는 크게 변하지 않으며 본체와 트림을 위한 재질선택은 밸브입구의 속도에 기초할 수 있다.
(3) 볼 밸브와 프러그밸브(Ball and plug valves)
(가) 볼밸브와 프러그밸브는 본질적으로 90°를 회전시켜 빠르게 열고, 닫을 수 있다.
(나) 밸브에 사용하는 고무나 플라스틱 재질은 단열압축에 의한 문제가 발생할 수 있다. 또한 볼은 일반적으로 닫히거나 열릴때 흐름경로에 날카로운 모서리가 있어 주의하여야 한다.
(다) 볼이나 플러그가 완전히 열리면 유체흐름이 매끄러워 본체 및 트림은 비충돌유체로 간주된다.
(라) 볼밸브와 프러그밸브는 서서히 작동될 수 있도록 기어식 조작핸들을 설치한다.
(4) 버터 플라이 밸브(Butterfly valves)
(가) 나비형 밸브는 개방시 밸브 디스크가 유체내에 있는 상태로 작동한다. 밸브와 디스크사이에 엘라스토머씰 또는금속 대 금속시트를 사용하여 누설을 방지한다.
(나) 나비밸브가 활짝 열리면 흐름이 매끄러워지고 차체는 충돌하지않는 부위로 간주될 수 있으나, 그렇지 않으면 충돌면으로 간주된다.
(다) 버터플라이밸브는 서서히 열도록 기어식 조작핸들을 설치한다.
(5) 게이트 밸브
(가) 게이트 밸브가 완전히 열리면 밸브를 통과하는 흐름이 매끄러운 것으로 간주되고 본체는 충돌하지않는 부위로간주될 수 있으나, 그렇지 않으면 충돌면으로 간주된다.
(나) 게이트와 본체시트 사이, 게이트와 백시트(backseat) 사이, 회전하는 스템과 게이트 사이 스템나사산과 가이드사이등의 게이트 밸브의 움직이는 부분에서는 잠재적으로 마찰표면이 존재한다.
(다) 만약 게이트 밸브가 닫힌상태에서 우회밸브를 열어 압력을 밸브 전후의 압력과 동일하게 경우도 일부게이트 밸브는 밸브 본넷(bonnet)의 압력이 낮게 유지될 수 있다. 이 경우 초기개방시 본넷 부위가 단열압축이 일어날 수 있다.
(라) 일부 게이트 밸브는 밸브시트를 용접이나 나사로 고정하는 경우에는 조립후 나사부위를 청소하기 어려울 수가있다.
(마) 게이트 밸브가 열리면 밸브 시트 자리에 금속부스러기와 같은 이물질이 끼이게 할 수 있다.
(6) 글로브밸브
(가) 글로브 밸브는 일반적으로 제어용도로되며 일반적으로 자동으로 운전된다.
(나) 글로브 밸브는 유로가 구부러져서 많은 충돌면을 가지고 있다.
(다) 트림설계는 제조업체마다 달라질 수 있지만 누설방지와 시트 손상방지를 위하여 얇은 탄성체나 플라스틱이 장착되어 있을 수 있다. 경우에 따라서는 케이지 트림(Cage trims)이 사용되는데 이 트림이 금속같이 이물질이 끼이고, 전단기 역할을 할 수 있다.
(라) 밸브 본체와 트림을 조절하는 특성을 갖는 글로브 밸브는 충돌면으로 간주하고, 면제재질을 사용하여야 한다.
(7) 안전밸브
(가) 안전밸브는 본질적으로 유체가 고속으로 흐른다.
(나) 안전밸브 본체와 출구배관은 충돌이있다.
(다) 밸브와 트림의 크기는 입구측의 유속을 낮게 유지하기 위하여 선정한다.
(라) 밸브 본체와 트림은 충돌면에 해당되어 특별하게 다른 경감대책을 수립하지 않으면 시트와 트림은 면제재질을사용해야 한다.
(마) 안전밸브는 국내 관련 법령 등에 따라 제조, 설치 및 유지보수가 되어야 한다.
(8) 체크밸브
(가) 체크밸브는구조적으로 항상 유체가 흐르고, 빠른 유속과 충돌면을 가지고 있다.
(나) 그러므로 체크밸브의 디스크, 트림, 플레이트, 피스톤, 스프링 등은 면제재질을 사용해야 한다.
(다) 밸브의 유형에 따라 체크밸브의 동체가 출돌지점으로 간주될 수 있고, 그렇지 않을 수도 있다.
(라) 트림설계는 특정 공급업체에 따라 다르지만, 누출 및 시트 손상을 최소화하기 위해 상대적으로 얇은 섹션으로 엘라스토머/폴리머인서트가 장착되어 있을 수 있습니다.
(마) 체크밸브 부품은 서로 충돌하게 설계되어 잠재적인 점화원과 입자생성의 원인을 제공할 수 있다.
(바) 특별한 완화조치를 하지 않으면 유체가 흐르는곳에서 움직이거나 충돌요인있는 부품은 부록2에 표시된 두께이상인지를 확인하여야 한다.
(사) 왕복식 압축기의 다운스트림에 사용되는 플레이트 체크밸브는 맥동흐름이 있어 위험성평가를 실시하여야 한다.
(아) 체크밸브는 떨림을 적게 설계하고, 떨림이 최소화 되도록 설치하여야 한다.
5.3.4 Valve seals and packing
(1) 산소를 취급하는 설비에서 사용하는씰이나 패킹구매자는 설계조건에서 적합한 재질 선정지침에 따라 제조자에게 확인하여야 한다.
(2) 비금속재질의 씰과 패킹의 호환성에 대한 정보는 ASTM G63에서 확인할 수 있다.
5.3.5 기타가능한밸브점화원
(1) 금속구성요소간마찰로인한국소가열
(2) 서로다른전위차에서두금속부품에서비금속절연물질로분리된아크방전
(3) 탄성체나플라스틱의진동으로탄성체나플라스틱의온도가국부적으로상승하고,유체의마찰에의해점화되고연쇄반응
(4)예를들어밸브조작기어박스나핸들휠에서사용하는산소와 부적합한그리스나윤활유등을사용할경우오일이나그리스 등이산소취급설비로이동하는것을방지하거나적절한안전거리를유지하여야한다.
5.4 배관부속설비
5.4.1 일반사항
(1) 산소취급설비에서 필터, 스트레이너, 오리피스 플레이트, 벤투리 유량계, 열전대관, 소음기 및 플렉시블(Flexible) 연결부 등이 해당된다.
(2) 배관에 설치된 대부분의 설비는 충돌을 일으킬 수 있어 설비별로 다음사항을 준수하여야 한다.
5.4.2 원뿔형 스트레이너(Conical strainers)
(1) 산소 취급설비에서 원뿔형 스트레이너는 일반적으로 스크린 메쉬(mesh)를 원뿔형으로 설치하여야 한다.
(2)스트레이너는 스크린 메쉬의 원뿔끝이 하류쪽으로 향하도록 설치하여야 한다.
(3)스트레이너 성능은 150㎛ 이상의 이물질을 제거시킬 수 있어야 한다.
(4)스트레이너의 메쉬는 직접적으로 이물질과 충돌할 수 있고, 이물질과 파편이 쌓여있어 고위험 영역에 해당된다.
(5) 와이어 메쉬(Wire mesh)는 표면비와 부피비가 얇은 소재로 제작되어 산소설비에 사용하기에는 화재가 발생할수 있다.
(6) 와이어메쉬(Wire mesh) 지지대 재질은니켈, 청동 또는 모넬과 같은 내화성 재질이어야 하고, 스테인리스강 재질은 내화성이 낮아 사용할 수 없다.
(7) 천공된 지지대는 <그림1>와 부록2에서 표시된 충돌속도곡선을 이용하여 재질선정과 충돌 면두께를 선정하여야 한다.
(8) 원뿔형 스트레이너 좌굴압력
(가) 원뿔형 와이어메쉬(Wire mesh)는 안전밸브 설정압력에서 좌굴되거나 붕괴되지 않도록 설계되어야 한다.
(나) 차압경보장치를 설치하여 차압이 좌굴압력미만에서 작업자에게 경보하여 적절한 조치를 하도록하여 원뿔 메쉬의 파손을 방지하고, 이물질과 파편 통과를 방지하여 잠재적인 화재의 위험을 방지하여야 한다.
(9) 원뿔형 스트레이너 설계
(가) 원뿔형 스트레이너는 역류 가능성이 없도록 설계되어야 한다.
(나) 기타 자세한 배관과 밸브의 요구사항은 5.4.4 필터를 참조한다.
5.4.3 Y형스트레이너(Y-type strainers)
(1) Y형스트레이너 본체는 충돌면과 정체구간에 해당되고, 오염물질이 점화되어 주위 구성품을 점화시킬 수 있는것으로 간주된다.
(2) Y형스트레이너 사용은 오염의 가능성이 낮은곳에 제한적으로 사용하여야 한다.
(3) 본체는 면제재질을 사용하여야 하고, 탄소강은 사용을 금지하여야 한다.
(4) 와이어메쉬(Wire mesh)와 스크린은 5.4.2의 원뿔형 스트레이너의 지침을 준수하여야 한다.
5.4.4 Y형스트레이너 본체에 있는 블로우다운 밸브(Blowdown valves)는 산소공급을 금지하여야 한다. 블로다운 밸브에 산소를 공급하면 청소하기는 쉬우나, 너무 빠른시간에 쉽게 열릴 수 있고, 국부적으로 빠른 유속에서 산소농도가 높아 위험할 수 있다.
5.4.5 필터(Filter)
(1) 필터에 여과된이 물질이 쌓이면 필터 에리먼트를 가스로 청소하여야 한다.
(2) 필터 위험성(Filter risks)
(가) 필터 엘리먼트는 이물질이 쌓여 위험도가 높은 충돌면이 있다.
(나) 엘리먼트는 표면적 대 부피비가 높아 사용하는 재질에 따라 쉽게 점화될 수 있어 재질선정에 주의하여야 한다.
(다) 필터는 역류 가능성이 없도록 설계되어야 한다.
(3) 필터엘리먼트 재질
(가) 일반적으로 다음과 같은 재질을 사용한다.
(나) 유리섬유 또는 유기접착제가 없는 유리섬유의 직물
(다) 니켈직물이나 소결니켈
(라) 황동, 청동, 구리 또는 모넬400
(4) 유리섬유 필터 엘리먼트필터
(가) 엘리먼트가 유리섬유와 같은 비금속 산소 호환성 재질로 설치된 경우 매체에 정전하가 누적되지 않도록 구리선을 사용하여 접지되게 조립해야 한다.
(나) 제조할때 사용한 윤활제나 기타 물질을 제거하기 위하여 철저한 세척을 하여야 한다.
(5) 필터 좌굴압력(Filter buckling pressure)
(가) 필터엘리먼트에 차압이 너무 크게 걸리면 좌굴에 의해 파손되면서 화재의 위험성이 있다.
(나) 필터엘리먼트가 완전히 막혔을때 최대차압에서 견딜 수 있도록 하거나, 차압경보장치를 설치하여 경보하여야한다.
(6) 필터하우징(Filterhousing)의 재질선정은 충돌이 있는 경우와 충돌이 없는 경우를 구분하여 <그림1>와 <그림2>에 표시된 속도곡선을 이용하여 결정한다.
(7) 필터에 대한 배관 및 밸브 요구사항
(가) 필터는 입구와 출구에 차단밸브를 설치하여 청소할때 제거할 수 있도록하여야 한다.
(나) 필터세척을 위하여 제거할 수 없는경우에서 복수의 필터를 병렬로 설치하여 각각의 필터마다 차단밸브를 설치하여야 한다.
(다) 벤트 밸브는 각각의 필터마다 필터 출구쪽에 설치하여야 한다.
(라) 필터는 매우 빠른속도로 이물질을 포집하므로 역류시키는장치를 설치하는것을 금지한다.
(마) 예를 들어 공정이 정지되었을때 사용하는 바이패스 배관은 설계유량과 유속의 20% 정도만 유지보수 기간동안에 사용하는 경우 고려할 수 있다.
5.4.6 유량측정장치
(1) 일반 요구사항
(가) 유량측정장치는 옥외에 다른설비나 배관과 격리하여 설치해야 한다.
(나) 차단밸브와 우회밸브(Bypass valve)는 유량계로부터 상당히 멀리 떨어져있어야 하고, 화재위험지역과 이격거리를 유지하거나 차단벽을 설치하여야 한다.
(다) 재질선정은 <부록2>에서 면제재질을 사용하거나<그림1> 표시된 충돌속도곡선의 기준을 충족시키는 재질이어야 한다.
(라) 여과장치는 탄소강 재질의 유량측정 설비전단에 설치하여야 한다.
(마) 오리피스 유량계와 같은 정적인 유량계는 제조자의 요구사항을 충족시킬 수 있다면 동적인(움직이는 부품이 있는) 유량계보다 유리하다.
(바) 동적인 유량계는 일반적으로 전단에 여과장치를 설치한다.
(2) 오리피스 플레이트(Orifice plates)
(가) 오리피스 플레이트는관의 단면적보다 작은 통과 구멍을 가진 얇은 판을 관의 중간에 설치하여, 유체가 그 판을지날때에 생기는 전후의 압력차를 이용하여 유량을 측정하는 장치로, 단면적이 감소하여 유속이 빨라지고, 날카로운 부분(Sharp edges)은 충돌면에 해당하는 유량 측정장치이다.
(나) 면제재질은 <부록2>에서 해당하는 재질을 사용하여야 한다.
(3) 동적인 유량계
(가) 움직이는 부품이 있는 유량계의 설계와 선정은 산소설비의 압력, 온도 및 유량의 서비스 조건에 적합하여야 한다.
(나) Rotary, turbine, angular momentum mass flow, positive displacement 유량계 등은 광범위한 유량 측정범위와 정밀도가 높은 전형적인 동적인 유량계이다.
(다) 동적인 유량계는 과도한 압력, 빠른 유속, 역류 및 적정유량 초과 가능성을 고려하여야 한다.
(라) 동적인 유량계에서 특별하게 고려하여야 할 안전사항은 다음과 같다.
① 동적인 유량계를 설치하는 배관은 유량계에 전달되는 응력이 최소화되도록 설계·설치하여야 한다.
② 인력에 의한 유지보수작업은 안전작업절차에 따라서 산소공급을 중단, 전후단의 밸브차단, 감압등의안전조치를실시한 다음에 실시하여야 한다.
③ 윤활– 일부 동적인 유량계에 윤활유가 필요한 경우에는 다음 5.5에서 규정한 산소설비에서 사용이 가능한 윤활유중에서 선택하여야 한다.
④ 윤활유를 교환과 점검은 일정한 자격을 가진 작업자만이 수행해야 한다.
⑤ 원격지시계 – 적산지시계, 원격지시계는 유량계에 접근하지 않고 멀리 떨어진 안전한곳에서 읽을 수 있도록 설계되어야 한다.
⑥ 과속방지 – Rotary piston 유량계와 같은 동적인 유량계는 허용 최대유량을 초과하면 과도한 변형의 위험이 있어 과속방지조치를 하여야 한다.
(마) 움직이는부품이나 이물질의 접촉에 의해 발생하는 마찰은 걸림, 균열, 점화의 원인이 될 수 있다.
5.4.7 파열판(Bursting disks)
(1) 예상치 못한 고장, 산소 공급차질 등으로 고농도의 다량의 산소가 대기중으로 방출위험이 있어 산소공급이나 분배하는 배관에 파열판을 설치할때는 주의하여야 한다.
(2) 부득이하게 사용하는 경우에는 면제재질은 사용하여야 한다.
(3) 면제두께보다 얇은 스테인리스와 니켈합금은 파열판 설계조건, 설정압력에서 파열, 파열될때만 빠른유속이 가능하여야 한다.
(4) 파열조각이 발생하지 않는 파열판을 많이 선호한다.
(5) 대기와 접촉으로 부식되어 변형하는것을 방지하기 위하여 외부표면에 PTFE, FEP등을 얇게 코팅할 수 있다.
5.4.8 연결부 절연(Insulating joints)
(1) 연결부 절연은 유전체에 의한 두배관으로 구성된다.
(2) 연결부 절연의 목적은 음극방식 설비가 있는 배관과 없는 배관사이를 영구적으로 전기적인 불연속성을 제공하여야 한다.
(3) 이러한 전기적인 절연으로 연결부 절연은 줄효과(Joule effect)에 의한 가열로 인해 절연재가자연발화 위험이있다.
(4) 배관 내부에서 이물질로 인한 침적물이 두개의 배관을 연결시켜 일정이상의 전류가 흐르면 퇴적층이 가열되어 절연재가 점화되는 점화온도 이상이 될 수 있다.
(5) 산소와 접촉하는 절연재는 적절한 기계적 특성과 절연특성이 있어야 하고, 4.3의 규정을 만족시켜야 한다.
(6) 표준 플랜지를 사용하는 절연연결부는 다음과 같은 특징이 있다.
(가) 절연개스킷, 볼트와셔와 슬리브는 서비스 조건에서 산소배관에 적합한 재질이어야 한다.
(나) 개스킷, 볼트와셔와 슬리브의 절연내력은 제조자의 사양과 사용자의 요구사항에 따라 달라질 수 있지만, 일반적으로 10MV/m정도이다.
(다) 절연플랜는 수직배관에 설치하여 플랜지 내부의 표면에 이물질과 습기가 누적되어 절연 개스킷을 가로지르는 브리징을 최소화시켜야 한다. 이때 수직으로 부터45°까지는 기울어지게 설치할 수 있다.
(라) 개스킷의 내부직경은 배관의 직경과 같게 full-facetype으로 설치하여야 한다.
(마) 브리징 효과와 간극을 가로 지르는 아크의 가능성을 줄일 수 있도록 플랜지의 볼록 한면의 외경보다 개스킷 외경을 크게 설치하여야 한다.
(바) 절연 플랜지는 낙뢰에 의한 화재를 방지하기 위하여 고장전류 보호장치(Fault current protection cell)을 설치하여야 한다.
(사) 음극 부식 방지설비는 가능하면 외부전류를 제한하여야 한다.
(아) 절연 연결부는 스파크 또는 과도한 전압구배로 인한 접합부 틈새도는 절연재로 서로 다른 금속표면이 분리되는기타 위치에서 국소가열을 방지할 수 있도록 적절한 서지보호장치를 설치하여야 한다.
5.4.9 Flexible connections
(1) 산소배관설비에서 영구적인 Flexible connections, hoses, and expansion joints 사용은 두께가 얇고, 주름관에 이물질이 퇴적될 수 있어 사용하는것을 권장하지 않는다.
(2) 넓은 온도범위에서 사용하는 배관설비의 경우 배관의 온도팽창에 의한 변화는 팽창루프(Expansion loops)를설치한다. 팽창루프의 곡률경은 피그장치를 이용한 배관 내부 청소를 위한 청소용 피그장치(Cleaning pigs) 사용이가능하도록 선정하여야한다.
(3) 팽창루프의 재질은 5.2에서 요구하는 조건을 만족시켜야 한다.
5.4.10 기타설비
(1) 소음기(Noise reduction devices)
① 산소방출구에 설치하는 소음기의 동체, 방해판 및 확산기는 금속이나 콘크리트 구조이어야 한다.
② 금속은 내식성이 있어야 하고,<그림1>에서 면제속도곡선을 따라야 한다.
③ 소음기 조립체는 부품의 움직임이 없도록 설계되고 제작되어야 한다.
④ 흡음제를 사용하는 소음기의 재질은 불연성이 없어야 하고, 반드시 기름이나 그리스(Free of oil and grease)가없어야 한다. 이러한 물질의 예를 들면 유리섬유, 암면이 있다.
⑤ 스테인리스울은 배관이나 방출구의 소음기의 흡음제로 사용을 금지한다.
(2) 기타 부속품
① 산소와 접촉하는 기타 부속품은 <그림1>에서 면제속도곡선을 이용하여 선택한 재질을 사용하여야 한다.
② 비금속 재질은 4.3의 요구사항을 만족시켜야 한다.
③ 다음과 같은 부속품이 해당된다.
㉮ 압력센서 및 압력지시계
㉯ 공압 제어장치
㉰ 온도계 보호관(Thermowells)
㉱ 계장 도압관 및 차단밸브.
④ 흐름이 없는 작은 직경의 계장튜빙은 두께와 관계없이 스테인리스 튜브를 사용할 수 있으나, 밸브를 열어서 조절하는 계장밸브는 부록2에서 열거된 면제재질 사용을 고려해야 한다.
⑤ 계장 도압관은 정체구간을 최소화시켜 이물질의 축적을 방지하여야 한다.
⑥ 부르동관 압력계와 같은 다이얼계기는 부르동관이 파열되었을때 산소를 외부로 안전하게 방출시킬 수 있도록 압력 방출구나 파열판을 뒤쪽에 설치하여야 한다.
⑦ 유압류를 사용하는 감지기는 유압유가 산소와 직접닫지 않도록 4.3과 4.5의 규정을 따라야 한다.
⑧ 산소배관에 사용하는 압력센서와 지시계는 산소용(예를 들면 산소, 오일 또는 그리스 없음, 기름사용 금지, OXYGEN, NO OIL OR GREASE)임을 표시하여야한다.
5.4.11 방호설비(Protection systems)
(1) 압력, 유량 및 온도 스위치 및 기타장치를 포함한 방호설비의 설계 및 설치는 다음요소를 고려해야 한다.
(가) 기기의 품질 및 신뢰성
(나) 고장 및 영향모드(예 : 전원 고장, 계기공기고장, 계기회로고장)
(다) 트립및알람, 알람기능을 사용하는 경우에는 운전자의 대응능력
(라) 고장 고려사항과 공급 신뢰성 우려에 대한 고장 안전요구사항 및 결과
(마) fail-safe 요구사항과 신뢰성을 고려한 고장 안전요구사항 및 결과
(2) 모든 방호설비는 IEC 61505, 61511에서 규정한 SIL을 적용하는것이 권장된다.
5.4.12 열교환기
(1) 3㎜미만의 열교환기 튜브를 사용할때는 미량의 수분이 탄소강을 부식시켜 파멸적인 재앙이 될 수 있다는것의주의하여야한다. 따라서탄소강은열교환기의튜브로사용하는것을권장하지않는다.
(2) 열교환기 튜브는 면제합금을 사용하는것을 권장한다.
(3) 스테인리스 튜브는 <그림1>에서와 같이 산소속도가 낮은경우에는 사용할 수 있다. 이 지침은 외부 기화기 또는브레이징 알루미늄 열교환기는 적용범위에서 제외 되었음에 주의한다.
(4) 산소 압축기의 열교환기 재질은 EIGA Doc 10, 왕복 산소압축기의 재질은 EIGA Doc 27, 원심압축기의 재질은EIGA Doc 10과 EIGA Doc 27을 참조한다,
5.5 윤활유
(1) 모든 부품은 윤활유가 없이 작동되도록 설계되어야 한다.
(2) 다만 윤활유는 조립품 운전, 부품이나 장치의 작동에 꼭 필요한 경우에는 ASTM G63에서 규정한 윤활유를 사용할 수 있다.
(3) 윤활유는 윤활할 표면에 잘 접촉되고, 사용을 최소화시킬 수 있도록 엄격하게 관리되어야 한다.
(4) 윤활유는부품을조립할때한번만주입하고, 사용 중에외부로누출흔적이없어야한다.
(5) 산소 취급 설비에 사용하는 윤활유나 그리스는 일반적으로 산화 실리콘용액에 Halogenated chlorotrifluoroethylene(CTFE)을 혼합한것이다.
(6) 이러한 제품은 수분이 침투되면 심한부식을 일으킬 수 있어 건조한 대기에서만 사용하여야 한다.
(7) CTFE 윤활유는 알루미늄 표면과 반응할 위험이 있어 높은 토르크와 전단력이 작용하는 알루미늄 합금에 사용하지않아야 한다.
(8) CTFE 윤활유는 일반적으로 탄화수소를 기반으로 하는 윤활특성이 우수하지 않아 산소와 호환성이 있는 윤활유를 선정할때 주의하여야 한다.
(9) 윤활유나 부품고정제는 다음조건을 만족하면 사용할 수 있다.
(가) 최대운전압력이 103bar에서 자동점화온도가 400℃ 이상이거나, 운전압력이 120Bar보다 낮은경우
(나) 윤활유는 최대운전압력보다 50bar이상의 압력에서 ASTM G74방법으로 산소내에서 공압충돌시험을 통과한 경우
(10) 산소와 호환되는 윤활유는 탄화수소, 먼지, 기타 이물질에 의해서 조금이라도 오염되면 윤활유의 점화 저항력이 크게 감소할 수 있다는것에 주의하여야 한다.
(11) 감속기는 일반적으로 탄화수소계 윤활유를 사용하지만 누출된 산소가 일반 윤활유와 접촉되지 않도록하거나윤활유가 기체산소쪽으로 흘러가지 않도록 설계되어야 한다. 만약이와 같은기능이 보장되지 않는다면 산소와 호환성이있는 윤활유를 사용하여야 한다.
(12) 감속기의 윤활유 이동평가는 게이트나 글로브밸브의 스템이 이동하면서 설비내부의 산소와 접촉하는스템부분은 밸브설계에서 특히 중요하다.
(13) 운전중에 스템이 움직이면 밸브의 패킹을 통해서 탄화수소계 윤활유가 전달되어 외부 오염의 위험이 증가한다.
(14) 플랜지에 설치하는 볼트와 같이 산소와 직접 접촉하지 않는 윤활유는 산소와 호환되어야 한다.
6. 세척, 제조 및 검사
6.1 일반요구사항
6.1.1 세척원칙
(1) 배관설비의 세척은 설치 전에 모든배관을 사전에 청소하고, 시공중에 청결한 상태를 유지하거나 시공후에 배관 및 배관설비를 완전히 세척하여야 한다. 또는 앞의 두가지 방법을 조합하여 세척하기도 한다. 일반적으로 설치 전에세척하는것이 좋다.
(2) 배관을 설치하고 최종적으로 세척하여 완벽한 세척상태를 확인하는것은 비실용적이며 불가능하다.
(3) 따라서 프로젝트가 진행하는 동안 시공 및 세척에 관한 절차를 자세하게 문서화시켜 반드시 준수토록하여야 한다.
(4) 배관설비의 설계는 세척, 설치 및 시험방법이 상호 호환성이 있어야 한다.
(5) 재질준비와 시공단계까지 세척에서 청결상태검사를 위한 서면양식이 있어야 한다.
6.1.2 세척기준(Standard of cleanliness)
(1) 산소배관은 내부에 유기물, 무기물, 이물질이 허용기준에 부합하도록 제거되었을때 배관설비는 산소공급을 위해 깨끗한 것으로 간주된다.
(2) 허용 기준에 대한 지침은 6.5.4를 참조한다.
(3) 그리스, 오일, 스레드 윤활제, 먼지, 물, 파일링, 저울, 용접스패터, 페인트 또는 기타 이물질등의 오염물은 필수적으로 제거해야 한다.
6.1.3 세척방법
(1) 산소배관세척은 다음 방법중에서 하나 또는 둘 이상을 조합하여 실시하여야 한다.
(가) 산이나 알칼리를 이용한 화학적 세척 또는 보호막 형성
(나) 피그세척(Pigging)
(다) 기계적인스크래핑(scraping)
(라) 샌딩(Grit, sand, or shot blasting)
(마) 드라이아이스 브라스팅(Dry carbon dioxide ice blasting)
(바) 고압물세척
(사) 용제세척
(아) 고압세제세척
(자) 고온 세제세척
(차) 고속가스 퍼지.
(2) 피그세척(Pigging)은 일반적으로 배관 내부청소에사용된다.
(3) 사용 가능한 피그세척(Pigging)은 다음과 같은 광범위한 범주에 해당된다.
(가) 일반적으로 피그는 산소와 반응성이 없는 발포 성형물이나 고무로 제조한다.
(나) 따라서 발포성형물이나 고무를 사용한 피그장치는 이물질이나 파편으로 배관벽이나 배관내에 남아있지 않도록최대한 보장되는것이 중요하다.
(다) 남아있는 이물질이나 파편의 제거는 고속의 가스 퍼지에 의해서 제거가 가능하여야 한다.(6.3.7, 6.3.8참조)
(라) 그러나 다양한 청소단계에서 배관 내부 표면의 예상조건에 맞는 피그장치를 올바르게 선택하여 사용하면 피그장치가 손상되고 배관설비의 오염될 가능성을 최소화하여야 한다.
(마) 피그는 용제등의 세척제와 호환성이 있어야하고, 산소 공급표준에 따라 세척하는것이 중요하다.
(바) 피그장치를 사용하여 배관을 세척할때는 피그가 통과할 수 있도록 설계단계에서 배관의 곡률반경을 고려하여야 한다.
(사) 모든 피그 사용의 기록은 보존하여야 하고, 발사할때 마다 피그 수신장치에서 회수하여야 한다.
6.1.4 배관설비 및 배관구성요소
(1) 티(Tees), 밸브, 역지밸브(Check valves), insulation joints, regulators, meters,filters, and other fittings와 같은 배관구성요소는 사전에 산소공급이 가능하도록 사전에 세척된 것을 구매하고, 세척이 완료된 다음에 설치하여야 한다.
(2) 만약 산소공급에 적합하게 세척된 부품을 구매할 수 없다면 현장에서 규격에 맞게 세척할 수 있도록 준비하고, 세척하여야 한다.
(3) 배관부품의 육안검사는 설치하기전에 요구하는 규격에 적합한지를 확인하여야 한다.
(4) 분기배관과 평행배관은 세척을 위하여 별도의 설비로 취급하여야 하고, 세척이 완료된 후에 최종적으로 연결하여야 한다.
6.1.5 용접
(1) 배관부품은 산소배관에 적합하고, 승인된 용접방법으로 용접하여야 한다.
(2) 궁극적으로 내부 용접면이 매끄럽고, 용접비드, 슬래그, 금속조각이 없도록 내부 청결상태를 유지하는것이 중요하다.
6.1.6 내압시험(Pressure testing)
(1) 배관과 배관설비는 관련법규, 규정 또는 사용자 표준에 따라 기압 또는 수압시험을 하여야 한다. 일반적으로 기압시험을 많이 선호한다. (6.3.3참조)
(2) 어떠한 시험방법을 선택하든 해당 배관설비에 적합하고, 추가적인 작업이 없도록 경제적인 방법으로 편리한곳에서 압력시험을 실시하여야 한다.
(3) 배관설비는 시공한 법규에서 요구하는 압력으로 공압 또는 수압시험을 거쳐야 한다.
6.1.7 배관 부품설치
(1) 모든 부품들은 사전에 세척된것을 설치하여야 한다.
(2) 비파괴시험은 관련 KOSHA GUIDE를 참조한다.
6.2 배관설비 재질 및 사양
6.2.1 일반적인 요구사항
(1) 배관설비를 구매할때는 사전에 배관 세척방법과 절차, 배관설비의 재질 및 사양 등을 사전에 제조자에게 공식적으로 전달되어야 한다.
(2) 품질관리자료는 완전하게 추적이 가능하고, 관련자료를 구매자에게 제출하여야 하다.
6.2.2 관련법규, 규격 및 표준
(1) 일반적으로 제조공정, 재질, 등급 및 검사요건은 관련법규, KS, ISO 3183, API Specification 5L 등의 규격을 준수하고, 구매자의 요구사항을 준수하여야 한다.
(2) 배관재질의 화학적인 성분은 관련법규, 규격등을 준수하여야 한다.
(3) 설치하기전에 세척해야하는 파이프의 경우, 제조공정에서 파이프 내부표면에 녹이나 침전물 등이 발생하지 않는 방법으로 제조하는것을 권장한다.
6.2.3 배관제조공정
(1) 일반적인 제조방법은 무계목(Seamless, 無繼目, 이음매없는) 파이프, 고주파유도(HFI), 전기저항용접(ERW), 레이저빔 용접(LBW) 또는서브머지드 아크용접(Submerged ArcWelding, SAW) 등이있다.
(2) 구매자의 사전승인없이 다른공정에 의해 제조된 배관을 사용해서는 안된다.
(3) 파이프는 제작, 보관, 등의 과정에서 내부표면에 페인트, 니스 또는 래커와 같은 방식제를 도포하는것을 금지해야 한다.
6.2.4 열처리
(1) 파이프를 제작할때의 종방향 용접과(일반적으로 연속용접공정의 일부로 수행)또는 배관에 대한 열처리는 완료된 배관에 기본적으로 산화물층(酸化物層, 흑피)이 없도록 해야한다.
6.2.5 수압시험
(1) 현장에서 수행한 압력시험은 배관의 제조 및 품질관리 공정의 일부로 완성된 배관설비의 각 부분에 대해 수압시험 및/또는 와전류시험(재질의 규격에서 허용하는 경우)을 해야한다.
(2) 수압시험은 사용자의 특별한 요구사항이 없는 경우에는 관련 법규 등에서 요구사항을 따라야 한다.
6.3 사전 배관세척
6.3.1 일반사항
(1) 모든 배관은 대부분 녹이나 이물질 없도록 제작되고, 사전에 철저한 세척 및 청결상태가 유지되도록 밀봉하거나 포장된 상태로 반입되어야 한다.
(2) 세척방법은 경제성을 고려하여 기계적 또는 화학적 세척방법을 사용할 수 있다.
(3) 지하배관용 코팅배관은 외부 코팅공정이 내부표면의 세척기준을 훼손하지 않도록 예방조치를 실시한다면, 내부세척을 수행하기전 또는 후에 수행될 수 있다.
(4) 깨끗한 파이프는 오염을 방지하기 위해 파이프마다 개방단부는 세척 및 코팅후 씰링해야 한다(6.3.5참조).
6.3.2 파이프 제작
(1) 산소서비스를 위해 사전 세척을 수행하는 배관설비는 전체길이를 따라 육안검사를 할 수 있고, 필요한 경우 요구되는 표준에 따라 세척할 수 있는 방식으로 제작되어야 한다.
(2) 산소를 취급하는 배관의 제작 작업장은 다른 배관 작업장과 격리하여야 한다.
6.3.3 압력시험
(1) 배관설비의 압력시험은 다음조건을 만족한다면 기압으로 실시할 수 있다.
(가) 관련법규
(나) 설계코드
(다) 제3자의 내부규정(해당되는 경우)
(라) 공식적인 위험성평가에 기초한 허용 가능성.
(2) 기압시험 요건은 수압시험에 따른 산소배관의 오염 또는 부식의 위험을 최소화해야하는 필요성에 의해 결정된다. 하지만 어떤 이유로든 기압시험을 허용할 수 없는 경우 배관은 수압시험을 하여야 한다(6.1.6참조).
(3)수압시험 후에는 배수, 건조 및 점검이 필요하다.
6.3.4 내부표면처리
(1) 블로아웃을 포함한 사전 세척작업은 제작 시방서에 따라 실시되어야 한다‘
(2) 원하는 경우 제조업체의 시설(수압시험 후)에서 사전 세척 및 블로아웃을 수행할 수 있다. 단, 설치 전 보관기간 및/또는 보관조건(현장 이송포함)의 결과로 완성된 파이프의 내부표면 상태가 크게 악화될 가능성이 있는 경우 현장에서 사전세척 및 블로아웃을 수행해야 한다.
(3) 배관을 검사하여 필요한 청결기준이 달성되었는지 확인하고 가록을 유지해야 한다(6.5참조).
(4) 가벼운 인산염코팅을 적용하여 세척된 내부표면의 녹형성을 억제할 수 있다. 이는 화학 세척 절차 후 일반적인 관행이다.
6.3.5 운송준비작업
(1) 세척기준이 달성되면 배관의 개방단부에는 방진과 방수 밀봉이 가능하도록 견고하고 밀착된 피팅 플라스틱 캡(Fitting plastic caps)을 장착시켜야 한다.
(2) 캡은 튼튼한 접착 테이프로 고정하고 밀봉해야 한다.
(3) 보관기간과 운송조건에 따라 부식 최소화를 위해 각배관안에실리카 겔과같은포장된건조제를넣을수 있다.
(4) 건조제를 사용하는 경우, 설치 중에 용기가 파이프에 부주의하게 남아있지 않도록 보호하기 위해 플라스틱캡 내부에 단단히 고정시켜 보관하여야 한다.
(5) 현장 설치작업 중에사용되는건조제주머니의총수를확인하고문서화해야한다.
(6) 건조제 주머니를 제거할때 주머니가 손상되지 않았는지, 모든 주머니가 제거되었는지 주의하여야 한다.
(7) 작은구멍을 포함하여 배관의 모든 구멍은 금속 또는 플라스틱 플러그로 밀봉해야 한다.
6.3.6 청결유지
(1) 현장에 납품하기전에 세척한 파이프의 경우 현장의 육안검사 결과 어떤이유로든 배관의 청결도가 저하되지 않는한 설치 전에 배관의 추가 세척할 필요는 없다.
(2) 만약 청결도가 떨어진 경우에는 해당배관은 승인된 절차에 따라 공장 또는 설치 작업현장에서 다시 청소해야한다. 배관설치 중배관내부 표면은 깨끗하고 건조한 상태(즉,오일, 그리스, 토양, 이물질 및 유출수가 없는 상태)로 유지되어야 한다.
(3) 다음과 같은 내용이 포함된 현장 설치계획서에 따라 사전에 준비하여야 한다.
(가) 특히 배관이 통과하는 트렌치는 용접이나 개방된 파이프나 배관자재를 취급할때는 물, 가연성 물질등이 유입되지 않도록 깨끗하게 유지하여야 한다.
(나) 매일작업이 끝났거나, 작업을 하지 않을때는 개방된 배관은 압력 유지플러그 또는 용접캡으로 파이프의 개방된끝을 밀봉한다. 장시간 사용하지 않을 경우 추가적인 예방조치로 배관은 약 0.01MPa의 건조한 무유성(Oilfree) 공기 또는 질소로 가압하여 보관한다.
(다) 모든 배관의 마감용접은 작업을 시작하기전에 공인감독자가 배관내부를 육안검사를하여 기록하고, 향후 작업을 위하여 결과를 보존하여야 한다.
(라) 불활성 가스 퍼지장치의 청결유지(예: Lances, temporary seals)
(마) 작업자는 항상 깨끗하고, 오일 오염이 없는 작업복을 착용하고, 손에 오일, 그리스 및 과도한 오물이 없도록하여야 한다.
(4)시공기간 동안 배관은 대기에 개방될 수 있으며 이러한 노출로 인해 내부 표면부식이 어느정도 발생할 수 있다.
(5) 배관설치 작업이 끝나면 배관표면의 부식정도를 확인하고, 피그를 사용하여 제거하고, 고속으로 퍼지시켜 표면의 부식을 제거해야 한다.
(6) 탄소강 배관의 경우 관련법령이나 시방서에 범위내에서 가벼운 표면의 녹은 허용될 수 있다.
(7) 건설작업자는 항상 깨끗한 작업장에 있어야 하고, 오일이나 그리스를 사용하는 작업장에 출입을 금지하여야 한다.
(8) 산소 배관 작업장에서 사용하는공구, 기계 등은 오염되지 않도록 별도의 장소에 보관하고, 기록을 유지하여야 한다.
(9) 일반 작업장으로 이동한 공구, 기구 등을 재반입할 경우에는 관련 절차에 따라서 깨끗하게 세척하고, 기록을 유지하여야 한다.
(10) 윤활유를 사용할 경우에는 사전에 윤활유 사용을 통제하는 통제자의 승인을 받아야만 사용할 수 있다. 산소와 호환되는 윤활유의 선택은 5.5를 참조한다.
(11) 배관을 가압할때 사용하는 플러그는 깨끗하게 유지하고, 사용하지 않을때는 깨끗한 플라스틱 봉지에 보관하여야 한다.
6.3.7 최종세척
(1) 최종세척은 프로젝트 요건에 적합하도록 전체 시공 프로그램의 편리한 지점에서 수행한다.
(2) 세척절차는 무엇보다도 공사중 오염의 위험성, 잠재적 오염물질의 특성 및 세척전 또는 후 내압시험에 사용되는방법등 여러요인에 따라 달라질 수 있다.
(3) 어떤경우에도, 피그장치 사용은 배관설비에 남아있는 잔류 오염물의 특성과 정도에 따라 피그세척여부를 결정한다.
(4) 공기중에서는 불연성이지만 산소농도에 따라 가연성이 될 수 있어 세척제나 용매 사용시 주의하여야 한다.
(5) 만약 세척할때 화학물질,용제 또는 세제를 사용한 경우, 시운전 전에 액체 잔류물을 완전히 배출하고, 제거하는것이 중요하다. 사용 가능한 세척방법은 6.1.3을 참조한다.
6.3.8 누설시험 및 블로우 아웃
(1) 내부의 이물질이 제거된 배관설비는 설비의 설계압력에서 건조하고, 기름이 없는 공기 또는 질소로 누설시험을실시하고, 고속으로 블로우 아웃을 시킨다.
(2) 밸브, 오리피스 플레이트, 스트레이너, 필터 및 기타 사전 세척 장비 항목은 입자상 물질에 의한 손상 또는 오염으로부터 보호하기 위해 블로아웃 작업이 끝나고 설치해야 한다.
(3) 최종고속가스 퍼지는 잔류 이물질을 실질적으로 제거할 수 있을 만큼 높은속도(일반적으로 25m/s)로 실시한다.
(4) 퍼지가스 출구측에 알루미늄으로 만든 표적판을 설치하고 배출되는 이물질에의한 충돌흔적으로 판정하는것이효과적이다. 이때 사용하는 알루미늄판의 경도는 25∼35HB 정도 이다.(ISO 6505-1, 금속재료 — Brinell 경도 시험—제1부 : 시험방법 참조)
(5) 또한 고속가스 퍼지 출구측에 강판으로 만든 그리스 얼룩판을 설치하여 산소와 반응할 수 있는 그리스 등의 흔적을 확인하여 적정여부를 판정하여야 한다.
(6) 표적판은 가스퍼지방출구에서 직경의 0.5배 떨어진 곳에 견고하게 설치하여야 한다.
(7) 육안 또는 표적판의 흔적이 0.2㎜ 미만이거나 없을때까지 실시하여야 한다.
(8) 그리스 얼룩판은 육안으로 흔적이 없을때까지 실시하여야 한다.
(9) 질소를 퍼지가스로 사용하는 경우, 산소 결핍에 의한 질식사고예방을 위하여 방출구 위치와 방향설정에 주의하여야 한다.
6.4 설치 후 청소
6.4.1 최종세척
(1) 최종세척은 파이프는 일반적으로 6.2항에 따른 일정한 길이의 배관으로 사전에 제작되어 산소 취급설비의 설치장소에 설치한다.
(2) 제안된 세척방법으로 원하는 세척기준을 달성할 수 있는지는 제조자가 제출한 자재의 목록과 세척관련 시험 성적를 기준으로 배관의 세척상태(예: 표면의 산화물층, 흑피)를 확인하는것이 중요하다. 세척방법은 6.1.3을 참조한다.
6.4.2 압력시험
압력시험은 6.3.3을 참조한다.
6.4.3 내부표면마감
(1) 블로아웃을 포함한 세척하는 절차는 관련법규, 코드 및 사용자의 사양서등에 따라 실시하고, 적정여부를 확인하여야 한다.
(2) 배관설비는 세척기준에 적합한지를 확인하기 위해 배관내부를 검사해야 한다(6.5참조).
6.4.4 청결유지
배관설비는 설치하는 동안 이물질(예:오일, 그리스, 흙, 금속파편 및 유출수 등)의 유입을 최소화하기 위해 모든 노력을 하여야 한다.(6.3.6을참조한다.)
6.4.5 누설시험과 블로아웃
블로아웃이 필요한 경우 자세한 내용은 6.3.8을 참조 한다.
6.5 검사
6.5.1 검사절차
(1)시공,시험 및 세척과정이 만족스럽게 끝나면 배관설비는 내부표면의 상태를 평가하기 위해 입구와 배출단부 양쪽 및 접근 가능한 모든지점에서 배관 및 배관설비를 검사해야 한다.
(2) 필요한 경우, 품질관리절차에 따라 접근 가능한 모든 개구부에서 표백제로 처리되지 않은 흰색의 보풀없는(Lint-free) 천 또는 여과지로 배관 설비 내부 표면을 닦아서 표본을 채취할 수 있다.
(3) 필요한 경우 샘플링에 사용되는 와이퍼를 식별번호를 붙여 폴리에틸렌봉지에 밀봉한 후 배관 품질관리자료의 일부로 관하는것을 권장한다.
(4) 검사는 다음절차 중 하나 이상을 사용하여 수행해야 합니다.
(가) 백색광을 사용하여 내부표면을 육안으로 검사하여 세척이 효과적이고 회색금속 마감, 그리스, 녹, 슬래그 및 기타 이물질이 없는지 확인한다. 단 탄소강의경우, 가벼운 녹막은 허용될 수 있다.
(나) 자외선(UVA) 조명을 구멍에 비추어 내부에 기름이나, 그리스가 없는지 확인한다.
(다) 만약 천이나 여과지를 사용한 경우에는 밝은 흰색 조명 및 자외선(UVA) 조명에서 기름이나 그리스가 없는지를확인한다.
6.5.2 자외선 검사
(1) 자외선 검사가 필요한 경우 모든 샘플과 개구부를 적합한 자외선(UVA) 광원으로 검사하여 탄화수소 오염의 증거가 없는지 확인해야 한다.
(2) 자외선(UVA) 광선검사를 받을때 샘플이 형광을 나타내지 않는다면 샘플의 약간의 변색이 허용됩니다.
(3) 다음 기준에 따라 파이프 표면 또는 걸래에 있는 탄화수소 오염물질의 형광검출에 사용하는 자외선(UVA) 광원을 선택한다.
(가) 빛의 파장은 250∼400㎚ 사이이어야 한다.
(나) 광원은 30㎝ 에서 5.0㎽/㎠의 광도를 제공하는 적절한 필터와 수은 등이나 할로겐 램프를 사용하는 스포트라이트이어야 하다.
(다) 일반적으로 형광램프는 사용하지 않는다.
(4) 대부분의 경우 자외선 검사는 탄화수소의 오염정도에 대한 신뢰할 수 있는 지표를 제공하지만 모든 그리스나 오일이 자외선에서 발광하는 것은 아니다.
(5) 경우에 따라서는 배관설비의 제작, 장기보관 또는 현장설치 작업중에 다른방법으로 검사를 할 수 있다.
6.5.3 허용 기준
(1) 허용기준은 관련기준, 코드, 사용자의 기준을 따른다.
(2) 허용기준이 확실하지 않을 경우에는 EIGA Doc 33/06, Cleaning of Equipment for Oxygen Service, European Industrial Gases Association, CGA G-4.1, Cleaning Equipment for Oxygen Service, Compressed Gas Association, and ASTM G93-96, Sections 9 and 10 등을 따른다.
6.5.4 시정조치
(1) 사전 세척 또는 현장 세척 과정에서 허용 가능한 세척기준에 부적합 증거 인심한 부식, 접착된 입자상 이물질, 오일, 그리스 또는 이와 유사한 탄화수소 오염의 징후를 피깅할때 찾아 관련 대책 및 세척기준을 함께 제출하여야 한다.
(2) 세척기준에 부적합 경우에는 다시 세척을 하여야 한다.
6.5.5 밀봉, 치환 및 모니터링(Sealing, purging, and monitoring)
(1) 배관 및 배관설비의 검사와 세척기준에 적합하면 모든 개방된 배관의 끝단을 모두 밀봉해야 한다.
(2) 배관설비의 검사가 끝나면, oil-free 공기 또는 질소로 내부의 이슬점이 –40°C 이하가 될때까지 치환시켜야 한다.
(3) 산소함량과 이슬점이 요구되는 수준에 도달한 후에는 건조하고, oil-free 공기 또는 질소로 배관설비를 밀봉하고 약 0.01MPa까지 가압해야 한다.
(4) 압력은 정기적으로 모니터링 되어야 하며, 사용하기 전까지 이상태로 유지되어야 한다.
6.5.6 기록
산소 공급 배관설비에 대한 청소활동과 검사 세부 사항은 관련법령, 지침 등에 따라 사전에 계획을 수립하고, 각종검사 기록을 관련자가 서명하고, 기록을 유지해야 한다.
7. 운영, 모니터링 및 유지보수
7.1 일반안전지침
(1) 배관설비의 작업은 사전에 안전작업허가서를 발급하고, 작업하여야 한다.
(2) 안전작업허가서에는 다음사항이 포함되어야 한다.
(가) 흡연은 작업지역에서 안전거리 5m금지
(나) 작업지역내에서 화기작업금지
(다) 오일이나 그리스의 흔적이 완전하게 제거되었는지 확인
(라) 용접장치의 접지금지
(마) 낙뢰가능성이 있는 경우에는 접지 설비 점검금지
(바) 낙뢰가능성이 있는 경우에는 작업자가 산소설비 주위에 접금금지
(사) 다른 배관설비는 근처 전력선의 접지결함으로 인해 발생하는 교류유도전류에 대한 위험을 방지하기 위하여 사전에 접지를 권장
7.1.2 운전자 및 유지보수자
(1) 산소 배관설비의 위험성 및 안전요구사항 등을 사전에 교육을 받아야 한다.
(2) 배관설비의 특성, 밸브 및 계측제어 설비 등의 위치를 잘 알고 있어야 한다.
(3) 운전자 및 유지 보수자는 모든운전, 정비, 안전운전, 유지보수 등의 절차서를 사전에 교육을 실시하고, 잘 알고있어야 한다.
(4) 협력업체 작업자 등은 사전에 산소설비의 유해위험성, 주의사항, 비상시 행동요령 등을 충분한 안전교육을 실시하여야 한다.
(5) 모든 작업자는 보푸라기가 없고, 기름이나 그리스 등이 없는 깨끗한 작업복과 장갑을 착용하여야 한다.
7.1.3 차단밸브 작동
(1) 제어벨브는 큰 압력차이로 작동되어 면제재질을 사용하여야 한다.
(2) 면제재질을 사용하지 않은 차단밸브는 사전 안전작업절차에 따라 바이패스 밸브 또는 기타 특정절차에 따라 차압을 최소화한 후에만 작동하여야 한다.
(3) 차단밸브가 현장에서 제어할 수 없는 원격으로 제어되는지 여부에 관계없이 차단밸브의 압력차이를 모니터링할 수 있는 조치를 하여야 한다.
7.1.4 용접 및 절단작업
(1) 산소 배관설비의 용접작업은 국부적인가 열도 점화원을 제공할 수 있어 사전에 철저한 안전조치를 하기전에는 절대로 금지한다.
(2) 산소배관 설비는 가능한 사전에 압력을 제거하고, 불활성가스로 치환하고 작업하는것이 좋다.
(3) 사전안전조치는 다음과 같다.
(가) 배관설비 내의 압력을 제거하고 작은 구멍을 뚫는작업
(나) 다음과 같이 스터드 용접장치를 사용하여 음극 보호스터드 용접
① 배관의 재질과 특성을 잘이해하고,
② 볼트가 용접되는 동안 배관 내부에 열이 거의 발생하지 않거나 전혀 발생하지 않도록 안전작업절차서가 있고, 관련된 절차에 따라서 안전한 용접을할 수 있는 용접장치가 있고,
③ 안전한 용접작업을 할 수 있는 자격을 가진자가
④ 안전작업절차서와 안전작업을 감독하는 감독자의 지시에 따라 작업을 수행하여야 한다.
7.1.5 산소농도
(1) 산소배관설비의 주위작업은 통풍이 잘되는곳에서 수행하여야 한다.
(2) 산소농도는18.0∼23.5%이어야하고, 다음의 제한사항을 준수하여야 한다.
(3) 산소농도가 낮은 경우에는 질식의 위험이 있다,
(4) 산소농도가 높은 경우에는 화재폭발의 위험이 증가한다.
(5) 낮은온도의 산소가 누출되면 낮은곳으로 산소가 모여, 23.5% 이상의 산소농도가 될 수 있다.
(6) 불을 사용하여 산소농도를 확인하는것은 절대로 금지한다.
(7) 작업장의 산소농도는 산소농도 측정기를 사용하여 측정하고, 정기적으로 교정하여야 한다.
(8) 기타 자세한 사항은 KOSHA GUIDE P - 138 – 2013“산소 과잉 분위기의 화재 위험성 및 방지대책에 관한 기술지침”, H - 80 – 2018“밀폐공간 작업프로그램 수립 및 시행에 관한 기술지침”을 참조한다.
7.1.6 배관설비 정지와 운전
(1) 배관설비의 정지와 운전은 안전운전절차서를 작성하고, 절차서에 따라야 한다.
(2) 안전운전절차서는 운전자, 유지 보수자 및 협력업체 관계자에게 산소의 유해 위험성 및 안전작업절차 등을 교육하여야 한다.
(3) 관리감독자는 다음사항을 확인하고, 단계별로 반드시 승인하여야 한다.
① 안전운전절차서 및 작업범위가 문서로 확정되었는지?
② 작업자의 안전보건교육을 실시하였는지?
③ 안전작업허가서는 적정하게 발급하였는지?
④ 유지보수작업을 시작하기전에 차단절차가 안전하게 이루어졌는지?
⑤ 배관을 다시 가압하기전에 유지보수 작업이 완료 되고, 산소공급을 위한 세척작업이 규정에 맞게 수행하였는지?
(4) 작업영역이 완전하게 차단될때까지 정비작업을 수행할 수 없다.
(5) 차단작업이 필요 없는 배관작업 또는 가열이나, 화기작업이 없는 작업중에서스트레이너의 이물을 제거작업과 같은 배관 구성요소에 대한 유지관리를 수행할때는 배관설비를 안전하게 감압할 수 있는경우 단일밸브를 닫아 격리할 수 있다.
(6) 체크밸브는 유지보수 작업을 위한 차단장치로 사용할 수 없다.
(7) 절단이나 용접과 같은 주요 작업은 다음과 같이 확실하게 차단작업을 실시하여야 한다.
① 해당 배관설비의 공정을 완전하게 분리(complete disconnection)
② 맹판(blind flanges) 설치
③ 이중밸브를 모두 닫고, 두 밸브 사이의 벤트밸브를 개방(이때 모터 작동밸브는 전원을 공급하는 결선분리)
④ 장비가 차단되었거나 맹판이 설치되었음을 알리는 태그를 부착
⑤ 산소농도를 지속적 일정한 시간마다 측정하고 기록
⑥ 개방된 산소설비는 이물질에 의한 오염을 방지하기 위한 밀봉
7.1.7 대기방출과 압력제거
(1) 대기방출
① 대기방출은 건물, 설비 및 작업자와 멀리 떨어진 안전한곳에 방출시켜야 한다.
② 내연기관으로 작동하는 콤프레셔 및 차량근처에 방출을 금지한다.
③ 고전압전선근처에 방출을 금지하여야 한다.
(2) 압력제거
① 감압할때 유량을 조절하는 보조밸브는 실제 방출하는 차단밸브 이후에 설치한다.
② 보조밸브는 밀폐기능이 보장되어야 한다.
③ 보조밸브는 차단밸브가 완전히 열릴 때까지 닫혀있어야 한다.
④ 위의 조치가 완료된 후에 보조밸브를 사용하여 방출할 수 있다.
7.1.8 퍼징
(1)오일과 그리스가 없는 질소 또는 건조한 공기로 배관 설비내의 산소를 제거하여야 한다.
(2) 배관 설비 내에 산소가 남아있지 않도록 모든 분기관, 필터등을 포함하여 치환 프로그램에 따라 철저하게 치환을하여야 한다.
(3) 실내, 밀폐공간, 도랑 등은 환기팬을 사용하여 깨끗한 공기로 치환시켜야 한다.
7.1.9 작업공구등
작업에 사용하는 공구나 기계는 깨끗하고, 이물질, 기름이나 그리스가 없어야 한다.
7.2 시운전
(1) 산소설비나 장치의 시운전은 설비 제조업체의 지침, 관련법규, 지침 등을 따라야 한다.
(2) 지침에 따라 내압시험과 기밀시험을 실시하고, 산소를 공급할 수 있다.
(3) 가능하다면, 새로운 배관설비는다량의 건조한 오일 프리질소를 사용하여 플러싱 시켜 배관설비 내부의 이물질을 제거하여야 한다.
(4) 시운전이 시작되면 먼저 산소를 사용하여 내부의 공기나 질소를 제거시켜야 한다.
(5) 퍼징절차에 따라 압력을 받는 마지막 밸브를 조이거나, 우회 밸브(Bypass valve)를 사용하여 실시 한다.
(6) 산소순도를 보장하기 위하여 특정한 방향으로 퍼지하여야 한다.
(7) 산소의 순도는 산소농도 측정기를 사용하여 모든 출구에서 측정한다.
(8) 적정산소 농도가 유지되면 방출밸브 등을 닫는다.
(9) 배관설비가 퍼지되고, 방출구가 닫히면 배관을 우회밸브(Bypass valve), 압력조절 수동밸브 또는 제어밸브를 사용하여 서서히 배관설비 운전압력까지 가압한다.
(10) 시운전중에는 플랜지 연결부위등 에서 누출여부를 정기적으로 점검하고 기록하여야 한다.
7.3 작동 및 모니터링
(1) 산소설비나 장비는 제조업체, 관련법령, 지침 등에 따라야 한다.
(2) 배관설비 및 밸브 스테이션은 운전 및 안전운전절차서에 따라 양호한 작동상태로 유지되어야 한다.
(3) 운전자, 유지보수자는 모든 안전 및 기술 모니터링 조치를 포함한 설비유지보수지침을 따라야 한다.
(4) 수행할작업은 운전, 유지보수 및 안전운전절차서에 구체적이고, 간단하게, 알기 쉽게 명시되어야 한다.
(5) 각종검사,측정 등은 관련 법규, 지침, 제조자의 지침,회사의 규정 등을 따른다.
7.4 문서관리 및 정보제공
7.4.1 일반사항
(1) 산소설비의 유지보수 작업중 안전사고는 기술, 운전사항에 국한되지 않고, 다양한 분야에서 발생되고 있다.
(2) 산소 배관설비를 보호하고, 설비의 신뢰성을 보장하려면 산소 배관설비의 위치, 인접한 곳에서 작업 및 새로운 산소 배관설비의 설치 등의 정보를 관련자에게 알리고, 관련 법규나 규정 등에 따라 현장에 유해위험성 등을 게시하여야 한다.
7.4.2 법규준수
(1) 산소 배관설비를 설치할 때는 관련 법규, 조례, 지침 등을 준수하여야 한다.
(2) 공동으로 사용하는 파이프랙, 지하 매설물 등은 설비의 위치를 알아볼 수 있도록 표시, 주의사항을 현장에 게시하여야 한다.
(3) 산소 배관설비 주위 작업자에게 사전에 유해 위험성을 알리고, 관련된 정보를 제공하여야 한다.
(4) 산소 배관설비 주위에서 수행하는 화기작업, 굴토작업 등의 위험한 작업은 안전작업허가서를 발행하고, 사전안전조치를 실시하고 작업한다.
(5) 산소 배관설비에서 위험한 상황이 발생하면 연락할 전화번호, 기타 방법 등을 현장에 게시한다.
(6) 안전작업허가서와 관련된 내용은 KOSHA GUIDE, P - 94 – 2019“안전작업허가 지침”을 따른다.
7.4.3 작업요약
(1) 산소 배관설비 근처에서 작업은 관리감독자의 서명을 받은 서면, 도면 등으로 지시하여야 한다.
(2) 작업내용은 해야할 작업 범위와 해서는 안되는 작업범위를 문서, 현장 설명 등을 통해서 확실하게 협력업체 작업자를 포함한 모든 작업자에게 알려야 한다.
(3) 작업구역은 바닥에 표시, 통제선 설치 등 구체적으로 표시하여야 한다.
7.4.4 기록
(1) 산소 배관설비 관리자는 다음사항을 기록하고 보존하여야 한다.
(가) 작업지시서, 계약서, 작업시방서, 안전작업허가서,회의록 등
(나) 작업자, 계약자의 요청사항
(다) 작업자, 계약자의 질의사항에 대한 회신문서
(라) 작업감독문서
7.4.5 문서관리
(1) 정확한 작업지시를 위하여 최신 자료나 도면을 사용하여야 한다.
(2) 산소 배관설비와 관련된 문서는 최신의 것으로 수정·보관하여야 한다.
(3) 새로이 설치하는 경우에는 기존의 도면에 표시하여 혼동을 방지하여야 한다.
(4) 설비가 변경된 경우에는 관련자료와 도면을 수정하여야 한다.
(5) 문서나 도면은 매년 현장설비와 일치하는지를 확인하고, 수정보완하여야 한다.
7.5 배관설비 손상관리
7.5.1 누출
(1) 배관설비에서 산소가 누출될 경우에는 즉시 보수하여야 한다.
(2) 산소누출이 의심되나 시각이나 청각으로 확인할 수 없는 경우에는 배관설비를 단위공정이나 설비별로 분리하여압력시험을 실시하여 안전하다는것을 증명하여야 한다.
7.5.2재검증
(1) 산소배관설비의안전성확보를위하여주기적인두께측정, 비파괴검사및유지보수, 세척등을실시하여안전하다는것을증명하여야한다.
(2) 누출, 화재 또는기타사고 등으로 배관설비의 수정, 교체, 대체한 경우에는 압력시험, 세척등을 실시하여 안전하다는것을 증명하여야 한다.
8. 일반안전조치
8.1 비상조치 계획
(1) 비상조치계획 문서는 협력업체를 포함한 모든 근로자, 방문자, 지역주민 및 공공기관을 포함하여 비상시 행동해야할 사항을 제공하기 위하여 작성되어야 한다.
(2) 단위설비나 공정별로 산소 배관설비의 특성을 고려하여 작성한다.
(3) 관련법령, 지침,회사의 방침 및 지역주민과 합의사항을 반영하여야 한다.
(4) 근로자, 지역주민, 공공기관, 협력업체 및 자문업체등의비상연락망을포함한다.
(5) 배관설비의 경로, 길이, 직경, 운전 및 설계압력, 유량, 차단밸브 위치 등을 도면, 관련자료를 포함한다.
(6) 배관설비가 심각하게 손상되면 전기방식을 분리한다. 만약 필요한 경우에는 임시로 결선한다.
(7) 비상시 통제센터 위치와 역할을 설정하고, 각자의 임무를 부여한다.
(8) 비상상황이 발생하면 협력업체를 포함한 사고 현장작업자, 방문자등에게 신속하고, 정확하게 알려야한다. 비상상황 대응절차에 따라 인접지역주민, 공공기관에게도 알려야 한다.
(9) 비상통제센터는 사고의 정확한 위치를 확인하고, 모든 상황을 기록하고, 비상대응팀에 정보를 전달할 책임이 있다.
(10) 비상상황에 대처하기 위한 장비는 적절한 위치에 즉시 사용이 가능토록 보관해둔다.
(11) 기타 비상조치계획은 KOSHA GUIDE P - 101 – 2012“비상조치계획수립에 관한 기술지침”을 따른다.
8.2 전원공급 설비 및 피뢰
(1) 배관설비가 고압전선과 평행으로 근접되어 설치된 경우에는 교류전류의 유도를 받을 수 있고, 철도와 근접되어설치된 경우에는 직류 또는 교류의 유도를 받을 수있다.
(2) 교류나 직류의 유도전류는 산소 배관설비를 여러개로 분할시켜 절연 플렌지 및 접지시켜야 최소화 한다.
(3) 기타 자세한사항은 KOSHA GUIDED - 51 – 2020“지하-지상 배관 연결부의 플랜지 절연장치 설치에 관한 기술지침”을 따른다.
8.3 화재
(1) 산소 배관설비에서 발생할 수 있는 특정 화재위험은 다음과 같다.
(가) 산소 배관설비 내부에서 화재가 발생하면 빠르게 확산된다.
(나) 일반적으로 이런화재는 몇 초후에 자동으로 꺼지지만 방출된 산소량은 산소가 풍부한 분위기가 형성될 수 있다.
(다) 산소가 풍부한 공기는 연소속도가 빨라질 수 있어 산소를 차단하고, 소화해야 한다.
(2) 산소 공급 화재를 처리하는 유일한 효과적인 방법은 산소공급을 차단하는 것이다.
(3) 산소가 풍부한 조건에서 적절한 소화방법은 물, 분말소화기, 이산화탄소 등이 있지만 화재의 종류에 따라 적절한방법을 선택하여야 한다.
(4) 산소농도가높은곳은구조자나작업자가움직일때발생하는정전기, 마찰등에의한작업복이점화되어화재가발생할수 있어, 산소농도가높은곳에진입하는것은위험하다.
(5) 산소농도가 높은곳에 있었던 작업자등은 담뱃불, 용접토치, 스파크 등의 점화원이 될 수 있는것을 멀리하고,옷을풀거나, 15분 이상 통풍이 잘되는 곳에 있어야 한다.
(6)화재가 발생하면 다음과 같은 조치를 상황에 맞게 적절하게 취해야한다.
(가) 신속한 상황판단(신속한 위험성평가)
(나) 화재경보 및 신고
(다) 위험지역을 이탈
(라) 산소 누출차단
(마) 재해자 구조
(바) 위험지역 통제
(사) 상황에 따라 근처 공장에 경보
8.4 사고 및 피해신고
(1) 산소 배관설비에서 사고가 발생하면 동종 또는 유사한 사고를 예방하기 위하여 철저한 조사로 사고원인을 규명하여야 한다.
(2) 보고서에는 사고전 몇 분 동안의 배관설비의 상태에 대한 정확한 설명이 포함되어야 한다.
(3) 기타 관련자료, 2차점화, 인명피해, 장비 및 재산손실 등의 사고결과를 기록한다.
(4) 산소 배관설비의 사고조사는 KOSHA GUIDE P - 106 – 2016“중대산업사고조사에 관한 기술지침”, ASTM G93, Standard Practice for Cleaning Methods for Materialand Equipment used in Oxygen-Enriched Environments 등을 참조한다.
8.5 안전관리체계
(1) 산소 배관설비는 관련 법규, 지침, 조례 등에 따라 관련된 인허가를 받아야 한다.
(2) 전반적인 설계 및 시공은 관련 법규, 지침, 조례 등을 준수하여야 한다.
(3) 비상정지는 누출 감지경보기, 경보설정값 등에 의해 자동으로 작동될 수 있고, 수동으로 정지시킬 수 있어야 한다.
8.6 운전
(1) 산소 배관설비의 제어전략은 설계범위 내에서 안전하게 제어될 수 있도록 설계되어야 한다.
(2) 제어전략은 다음사항이 포함되어야 한다.
(가) 압력
① 배관설비의 압력은 정확하게 측정되어야 한다.
② 내압력이 있게 설치한다.
③ 안전밸브를 설치한다.
(나) 배관설비에 극저온 액체가 유입되지 않도록 한다.
(다) 적절한 유속을 유지한다.
(라) 사양을 충족하지 않는 제품이 유입되지 않도록 한다.
(3) 산소의 폐기는 안전한곳에 대기 방출한다.
8.7 유지보수 및 검사
(1) 정기적인 예측 예방정비를 실시하여야 한다.
(2) 장거리 배관은 주기적인 순찰을 하여야 한다.
(3) 다음사항을 중점 확인하고, 기록을 유지하여야 한다.
① 방식 설비의 일상적인 시험
② 지상 플랜지의 육안누출점검
③ 배관 설비의 파손상태
④ 지반 침하상태
⑤ 배관설비의 인위적인 파손흔적
⑥ 배관설비의 위치 변경, 이탈, 고정상태
⑦ 안전운전 및 비상연락표지판 상태
[부록1] 공칭 합금 구성 및 범위
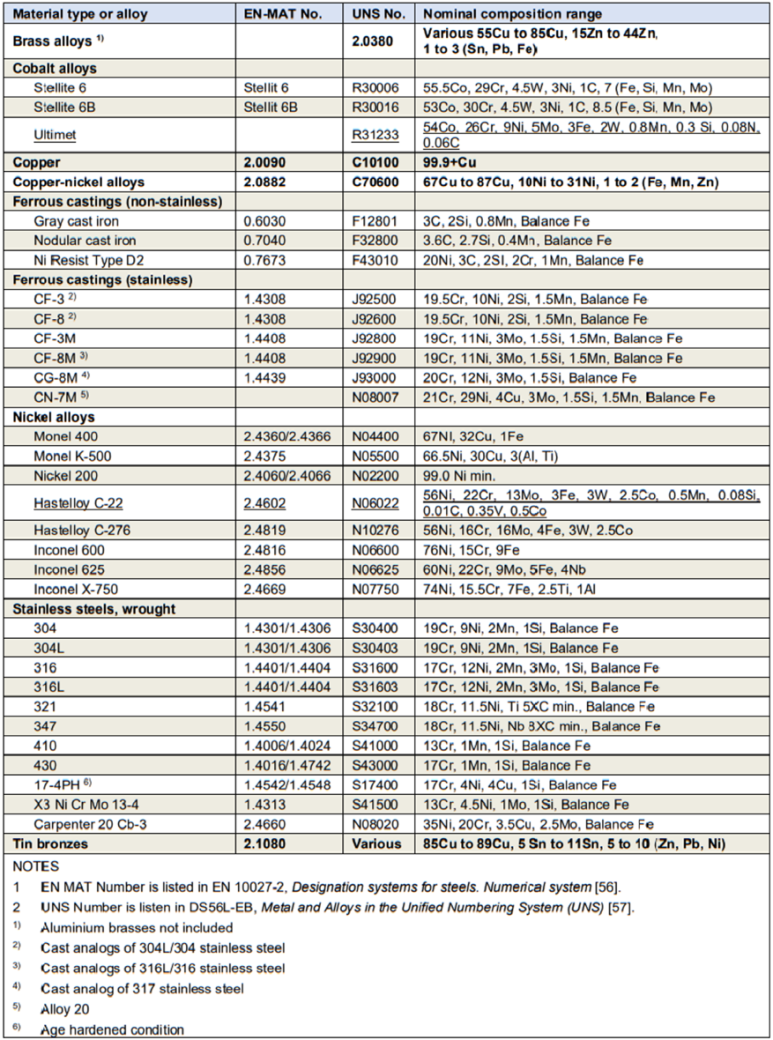
[부록2] 면제압력 및 최소두께
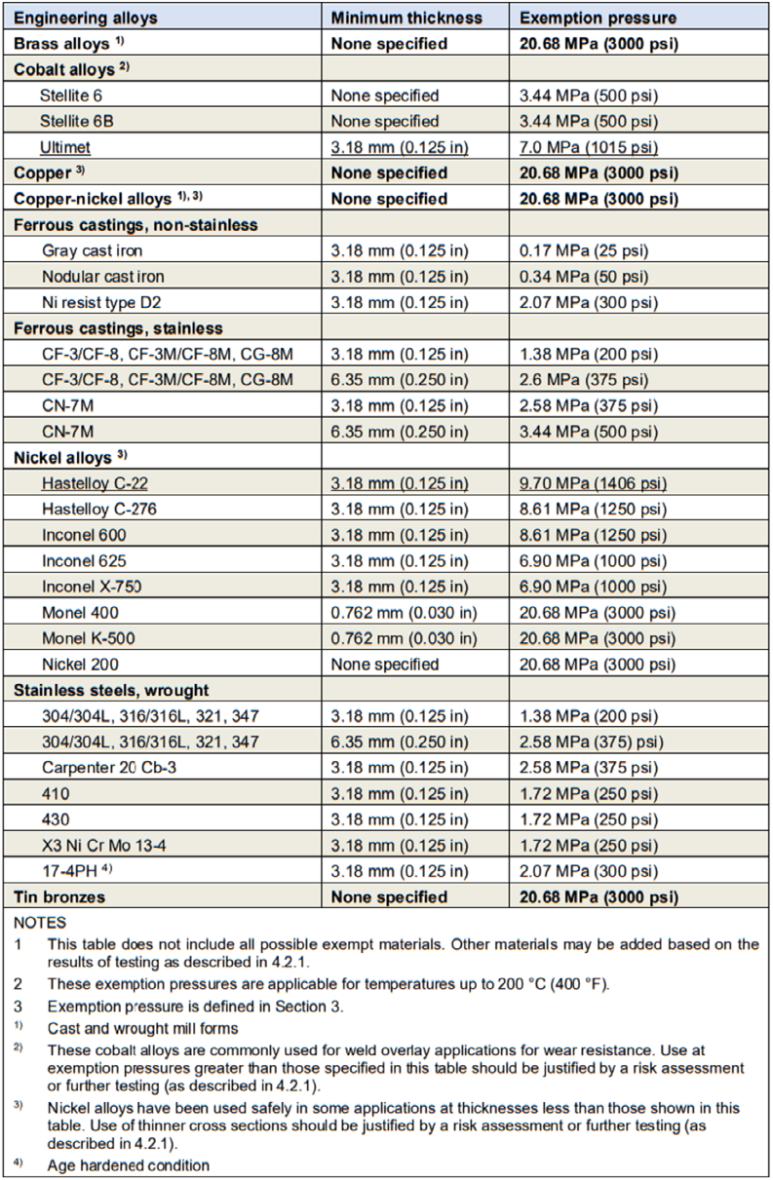
산소 배관 및 배관설비에 관한 기술지침(KOSHA GUIDE) - 2021.12
P – 170 - 2021 산소 배관 및 배관설비에 관한 기술지침(KOSHA GUIDE) - 2021.12. 1. 목적 산...
blog.naver.com
'·' 카테고리의 다른 글
반도체 공정에서 가스를 취급하는 벌크시스템의 안전에 관한 기술지침(KOSHA GUIDE) - 2012.11 (0) | 2023.03.14 |
---|---|
화학설비 고장율 산출기준에 관한 기술지침(KOSHA GUIDE) - 2013.06 (0) | 2023.03.14 |
방호계층분석(LOPA)기법에 관한 기술지침(KOSHA GUIDE) - 2012.07 (2) | 2023.03.14 |
산소 감지경보기 등의 설치 및 보수에 관한 기술지침(KOSHA GUIDE) - 2018.06 (0) | 2023.03.13 |
화학설비의 소방용수 산출 및소방펌프 유지관리에 관한 기술지침(KOSHA GUIDE) - 2012.07 (0) | 2023.03.13 |