D - 37 - 2012 화학설비 등의 공정설계에 관한 기술지침(KOSHA GUIDE) - 2012.07
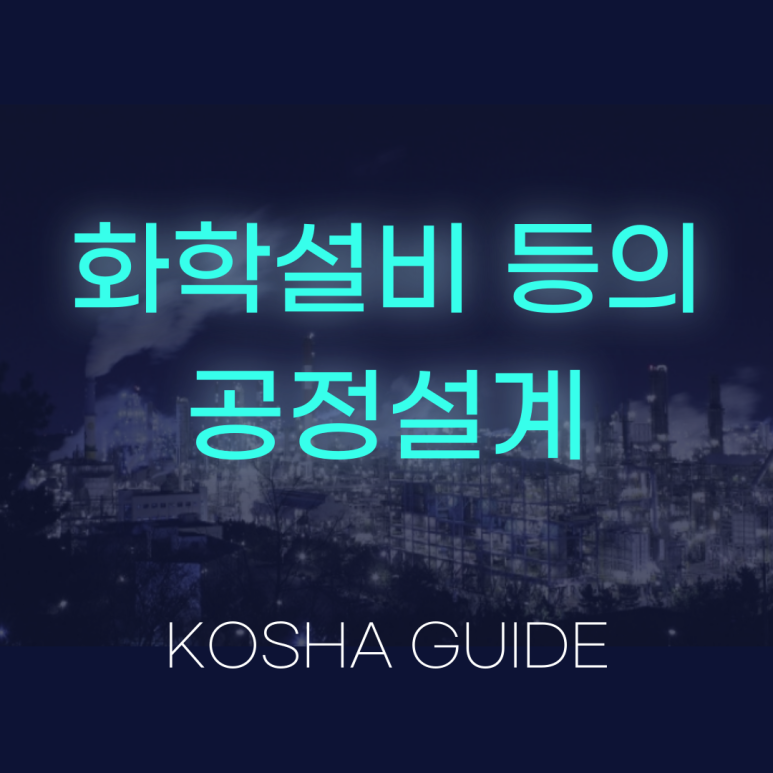
1. 목적
이 지침은 『산업안전보건기준에 관한 규칙』(이하 "안전보건규칙" 이라 한다) 제2장 폭발·화재 및 위험물누출에 의한 위험방지 제4절(화학설비·압력용기 등)의 규정에 의한 화학설비 등에 대한 공정설계기준을 정하여 화학설비의 대한 잘못된 설계로 인하여 일어날 수 있는 화재․폭발 및 화학물질의 누출 등에 의한 사고를 예방하는데 목적이 있다.
2. 적용범위
이 지침은 안전보건규칙 별표7의 화학설비 및 그 부속설비의 종류에 적용한다.
3. 정의
3.1 “공정용기(Process vessel)”라 함은 안전보건규칙 별표7의 화학설비중 “가”호 및 “나”호의 장치를 말한다.
3.2 “최대운전압력(Maximum operating pressure)”이라 함은 정상운전 중에 최대로 올라갈 수 있는 압력을 말한다.
3.3 “최대운전온도(Maximum operating temperature)”라 함은 정상 운전중에 최대로 올라갈 수 있는 온도를 말한다.
3.4 “유효양정(Net positive suction head)”이라 함은 펌프 흡입측에서 전체 양정과 펌프의 흡입구에서의 유체의 증기압에 상응하는 양정과의 차이를 말한다.
3.5 “슬러그 흐름(Slug flow)”이라 함은 기․액상흐름에서 액체파동이 주기적으로 거품덩어리 상태를 형성하면서 평균액체속도보다 빠른 속도로 움직이는 흐름을 말한다.
제2장 공정용기
4. 설계 및 제작 규격
(1) 모든 공정용기는 노동부 고시 『압력용기 제작기준․안전기준 및 검사기준』,『한국산업규격 KS B 6750 “압력용기(설계 및 제조일반)』 또는 미국국가기준협회규격 ANSI/ ASME Section Ⅷ 『Rules for construction of pressure vessel』 등의 최신판에 준하여 설계․제작되어야 한다.
(2) 안지름이 150 mm 이하인 공정용기는 전항의 규정을 적용하지 아니한다.
5. 설계조건
5.1 압력
(1) 최대운전압력이 게이지 압력으로 7 MPa(70 kgf/㎠) 이하인 공정용기의 설계압력은 최대운전압력에 최대운전압력의 10 % 또는 180 kPa(1.8 kgf/㎠) 중 큰 수치를 더한 수치 이상으로 하여야 한다. 가능하면 최소설계압력은 350kPa(3.5 kgf/㎠) 이상으로 한다.
(2) 최대운전압력이 게이지 압력으로 7 MPa(70 kgf/㎠)를 초과하는 공정용기의 설계압력은 최대운전압력에 최대운전압력의 5 % 또는 700 kPa(7 kgf/㎠) 중 큰 수치를 더한 수치 이상으로 하여야 한다. 다만, 파일럿 작동형(Pilot type) 안전밸브를 설치하는 경우에는 공정용기의 설계압력은 최대운전압력에 최대운전압력의 5 %를 더한 수치 이상으로 할 수 있다.
(3) 진공하에서 운전되는 경우에는 완전 진공에서 견딜 수 있도록 설계하여야 한다.
(4) 진공하에서 운전되지 않더라도 제어의 잘못 또는 열공급원의 차단 등으로 인하여 진공이 걸릴 수 있는 경우에는 완전진공에서 견딜 수 있도록 설계하거나 진공제거장치를 설치하여야 한다.
(5) 내부에 액체로 완전히 채워진 공정용기는 공정운전조건에 의하여 발생될 수 있는 진공을 고려하여 설계하여야 한다.
5.2 온도
(1) 일반적으로 설계온도는 정상운전온도에 30 ℃를 더한 수치로 한다. 공정용기의 전단에 수냉식 열교환기가 설치되어 있는 경우에는 냉각수의 공급이 중단되는 경우를 고려하여 온도를 결정하여야 한다.
(2) 고온․고압하에서 운전되는 반응기의 경우에는 온도증가에 따라 재질의 응력이 급격히 저하되므로 촉매의 사용기간 만료 직전에서의 예상되는 최대 운전온도를 고려하여 설계하여야 한다.
(3) 설계온도는 플랜지의 호칭압력을 결정하는데 영향을 주므로 이를 고려하여야 한다.
(4) 고온․고압용기인 경우에는 사용두께를 줄이거나 합금량을 줄이기 위하여 내부에 단열재를 설치할 수 있다. 이 경우 동체외부의 설계 온도는 150 ℃ 이하로 한다.
5.3 부식여유
(1) 일반적으로 부식성이 없는 유체를 취급하는 공정용기로서 일반 탄소강 재질을 사용하는 경우에는 공정용기의 사용기간을 10년으로 하여 3 mm의 부식여유를 준다.
(2) 부식성이 강한 유체를 취급하는 경우에는 부식에 대비하여 크래드강 또는 용접오버레이강(Weld overlayed steel)을 사용한다.
(3) 부식성이 강한 액체를 낮은 온도에서 취급하는 경우에는 공정용기의 내부에 내산시멘트 등으로 코팅하여 사용할 수 있다.
6. 공정용기의 크기
6.1 고정층 반응기
(1) 지름의 결정시에는 다음 사항을 고려한다.
(가) 반응기의 안지름은 사용하는 재질의 두께를 얇게하기 위하여 가능한 한 작게 하여야 한다.
(나) 정상운전중에 촉매층에서의 압력손실 및 촉매사용기간 만료시점에서의 촉매층의 오염 또는 막힘으로 인한 압력손실을 최우선적으로 고려하여야 한다.
(다) 제작장소로부터 설치장소로 운반시의 장애물을 고려하여야 한다. 이 경우 바깥 지름이 육상 운송인 경우에는 4 m, 해상운송인 경우에는 5 m 이하 가 되도록 하는 것이 좋다.
(2) 길이와 지름 비율은 약 3 : 1 정도로 하는 것이 좋다.
(3) 촉매층 위에서 촉매, 바스켓(Basket) 및 분배기(Distributor) 등을 설치하는데 지장이 없도록 촉매층 상부의 여유 공간을 충분히 고려하여야 한다.
(4) 촉매층 하부의 여유공간은 촉매지지대의 종류 및 특성과 우회(By-pass) 등을 고려하여 결정하여야 한다.
(5) 촉매층의 깊이가 긴 경우에는 동체는 열에 의하여 늘어나고 촉매층 자체의 깊이는 감소되는 현상(Slumping)을 고려하여야 한다. 이러한 현상은 높은 반응온도로 동체가 늘어나기 때문에 발생하며 촉매층은 깊이 1 m당 20
mm 정도가 줄어든다.
(6) 반응기 내부에 고온에 의한 동체의 재질을 보호하기 위하여 내화물의 설치가 필요한 경우에는 내화물 및 내부라이너(Liner)가 차지하는 두께의 2배를 감안하여 외부 동체의 지름을 결정하여야 한다.
6.2 증류장치
6.2.1 지름 결정시 고려사항
(1) 범람(Flood)조건의 85 % 이하에서 운전되도록 내부 지름을 결정한다.
(2) 제작장소로부터 설치장소로 운송시의 장애물 등을 고려하여야 한다.
6.2.2 단과 단 사이의 거리(Tray spacing)
(1) 단과 단 사이의 거리는 정비․보수를 위하여 600 mm로 하는 것이 좋다.
(2) 증류장치의 지름이 작거나, 취급하는 유체가 깨끗하거나, 단의 수가 40개를 초과하는 경우에는 단과 단 사이의 거리를 450 mm로 줄일 수 있다.
(3) 원료가 공급되는 단에서는 그단과 상부단사이의 거리는 최소한 600 mm이상이 되어야 한다.
6.2.3 상부의 여유공간
(1) 상부의 여유공간 즉 최상부 단으로부터 증류장치의 상부 탄젠트 라인(Tangent line)까지의 거리는 900 mm이상으로 한다.
(2) 증기의 토출관이 동체측에 설치되어 있는 경우에는 액체의 비말동반(Entrainment)을 방지하기 위하여 상부의 여유공간을 1200 mm이상 확보하여야 한다.
6.2.4 하부의 여유공간
(1) 증류장치 하부의 여유공간은 증류장치 내부에서 작업자가 서서 작업할 수 있도록 최소한 2100 mm 이상을 유지하도록 한다.
(2) 재비기(Reboiler)의 순환 노즐은 최하부 단의 밀봉접시(Seal pan)와 최대 운전액위 사이에 설치하여야 한다.
6.2.5 측면토출(Side draws)
(1) 증류장치 측면에서의 유체 토출은 서지시간(Surge time)이 필요없는 경우에는 하강유로(Downcomer) 바로 밑에 있는 단의 웰(Well)에서 하도록 하고, 서지시간이 필요한 경우에는 가운데 웰(Centerwell)에서 하도록 한다.
(2) 펌프의 흡입배관이 증류장치에 직접 연결되어 있는 경우의 측면토출은 가운데 웰(Centerwell)에서 하도록 한다.
(3) 가운데 웰(Centerwell)에는 증류장치의 내부 단면적의 12 % 이상의 면적을 갖는 증기파이프가 설치되어야 하며, 단으로 증기의 분산이 잘되도록 증기파이프의 끝단과 상부 단과의 사이는 충분한 여유를 가지고 있어야 한다.
(4) 증기를 측면에서 토출시키는 경우에는 축적파이프(Accumulator pipe)가 설치되어야 하며 단과 단 사이의 거리는 1500~2100 mm 정도 유지되어야 한다.
6.2.6 서지용량(Surge capacity)
(1) 증류장치 하부에서의 서지 용량은 정상 운전 액위로부터 최소 1분이상 유지되도록 하여야 한다. 일반적으로 정상액위로부터 2분 정도 유지되도록 한다.
(2) 증류장치 하부유체가 반응기 또는 정밀하게 분리시키는 증류장치로 인입되는 경우에는 증류장치 하부에서의 서지용량은 정상운전 액위로부터 5분이상 유지되도록 한다.
6.3 증류장치의 상부용기(Overhead receiver)
6.3.1 지름
(1) 상부용기의 지름은 증기 속도에 의하여 결정한다. 그러나 증기의 속도가 낮은 경우에는 액체의 체류 시간을 기준으로 결정한다.
(2) 증기의 속도는 다음 식에 의하여 계산한 수치 이하로 유지하도록 한다.
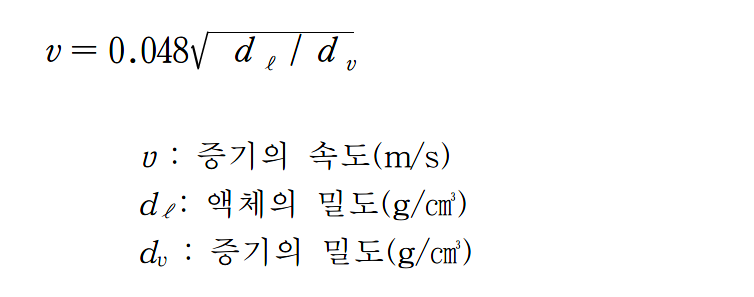
6.3.2 길이
(1) 일반적으로 상부 용기의 길이는 지름의 3배로 한다.
(2) 용기의 지름을 증기의 속도를 기준하여 결정한 경우에는 용기의 길이는 용기 내부에서의 액체의 체류시간을 기준하여 결정한다.
(3) 최소체류시간은 일반적으로 인입되는 양을 기준으로 5분으로 한다. 체류시간은 용기의 1/2이 채워진 상태를 기준으로 한다.
(4) 용기내부에서 비중차에 의하여 물의 침강(Settling)이 필요한 경우에는 취급하는 유체의 체류시간은 10~15분, 부츠(Boot)에서 분리된 물의 체류 시간은 5~10분으로 한다.
6.4 서지드럼(Surge drum)
6.4.1 충전 시간
서지드럼은 드럼을 75 % 채우는데 필요한 시간으로 결정하며 시간은 15~60분으로 한다.
6.4.2 길이와 지름의 비
드럼의 길이와 지름의 비가 3 : 1이 되도록 결정한다.
6.5 침강드럼(Settling drum)
6.5.1 침강시간
(1) 침강드럼은 침강시간을 기준으로하여 그 크기를 결정하며, 침강시간은 다음 사항의 함수이다.
① 유체의 비중
② 분리정도
③ 혼합정도
④ 기타 물리적 성질
(2) 침강시간은 다음식에 의하여 계산한다.
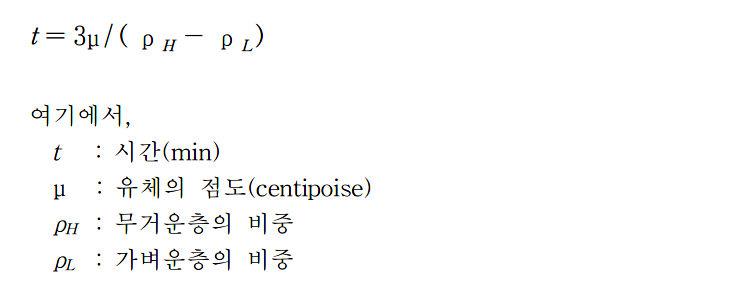
6.5.2 침강속도
유체의 침강속도는 다음식에 의하여 계산한다.
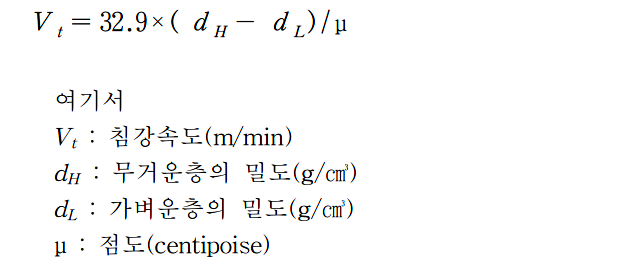
6.5.3 합체 블랭킷(Coalescing blanket)
(1) 합체블랭킷은 침강속도를 빠르게 하기 위하여 설치한다.
(2) 블랭킷을 통과하는 속도는 0.3~1 m/min로 한다.
(3) 블랭킷의 두께는 300 mm 정도로 한다.
6.6 기․액분리기
6.6.1 지름
(1) 기체의 유량을 기준하여 지름을 결정하는 경우에는 6.3.1항의 기준에 따른다.
(2) 액체의 유량을 기준하여 지름을 결정하는 경우에는 증기에 액체가 비말동반하는 것을 방지하기 위하여 그 속도를 30 mm/sec 이하로 하여야 하며 15mm/sec로 하는 것이 좋다.
6.6.2 체류시간
(1) 기체와 액체를 효율적으로 분리할 수 있도록 체류시간을 충분히 주어야 한다.
(2) 체류시간은 액위조절부유통(Level control float chamber)에서 최소한 조절밸브의 여닫음 시간의 5배 이상 이어야 한다.
6.6.3 미스트제거 패드(Demister pad)
(1) 기액분리기용 미스트제거 패드는 150 mm 두께를 일반적으로 사용한다.
(2) 최대 증기속도는 다음식에 의하여 계산한 수치 이하로 유지하도록 한다.

(3) 최소증기속도는 최대증기속도의 70 %이상 유지하도록 한다.
6.6.4 물의 침강
유체에 포함된 물을 침강시키는 경우에는 액체의 체류시간을 최소한 10분 이상 유지하도록 한다.
7. 공정용기의 모양
7.1 경판의 형태
7.1.1 타원형
일반적으로 2:1 타원형 경판를 주로 사용한다.
7.1.2 접시형
접시형 경판은 저압 공정용기에 사용한다.
7.1.3 반구형
반구형 경판은 설계압력이 게이지압력으로 7 MPa(70 kgf/㎠) 이상인 경우에 사용한다.
7.2 노즐
7.2.1 벤트노즐
(1) 모든 공정용기에는 공정 용기 또는 배관의 최상단에 벤트노즐을 설치하여야 한다. 단, 수소순환반응기는 그러하지 아니한다.
(2) 증류장치의 상부 용기에 설치되는 벤트의 크기는 비상시에 증류장치 내부 압력을 5분이내에 제거할 수 있도록 선정되어야 한다.
7.2.2 드레인 노즐
(1) 모든 공정용기에는 공정용기 또는 배관의 최하단에 드레인 노즐을 설치하여야 한다. 단 수소순환 반응기는 그러하지 아니한다.
(2) 증류장치의 드레인 노즐은 최소한 DN 40(NPS 1½) 이상이어야 한다.
7.2.3 액면계 노즐
(1) 모든 증류장치의 하부 및 기․액 또는 액․액 분리가 이루어지는 모든 공정용기에는 액면계 노즐을 설치하여야 한다.
(2) 액면계를 설치하기 위한 노즐은 DN 20(NPS 3/4)를 주로 사용한다.
(3) 액면조절 부유통을 설치하기 위한 노즐은 최소한 DN 40(NPS 1½) 이상이어야 한다.
7.2.4 노즐의 크기
(1) 노즐의 최대 크기는 공정용기 지름의 1/2을 초과하여서는 아니된다.
(2) 노즐의 최소 크기는 DN 20(NPS 3/4) 미만이어서는 아니된다.
7.3 맨홀
7.3.1 증류장치
(1) 모든 증류장치의 상부에는 DN 450(NPS 18)이상의 맨홀을 설치하여야 한다.
(2) 모든 증류장치의 원료공급단과 하부에는 DN 450(NPS 18) 이상의 맨홀을 설치하여야 한다.
7.3.2 증류장치 이외의 공정용기 맨홀
증류장치 이외의 공정용기에는 DN 450(NPS 18) 이상의 맨홀을 1개 이상 설치하여야 한다.
7.3.3 검사용 구멍
(1) 작업자가 검사를 실시하기 위하여 그 내부에 들어갈 수 없는 소형 공정용기에는 검사용구멍(Hand hole)을 설치하여야 한다.
(2) 검사용구멍은 그 안지름이 최소한 DN 150(NPS 6) 이상이어야 한다.
7.4 분배기(Distributor)
7.4.1 증류장치용
모든 증류장치의 원료 및 환류 노즐에는 분배기를 설치하여야 한다.
7.4.2 기타 공정용기용
(1) 수평형 공정용기에는 인입노즐 크기보다 한 치수 큰 수직관형 분배기를 설치한다.
(2) 수직형 공정용기에는 동체 가까이에 “T”형 분배기를 설치한다.
제3장 열교환기
8. 설계 및 제작 규격
8.1 스팀발생 열교환기
스팀발생 열교환기는 노동부 고시 한국산업규격 KS B 6750 “압력용기(설계 및 제조일반)” 또는 미국국가규격협회규격 ANSI/ ASME Section Ⅰ“Power boiler” 등의 최신판에 준하여 설계․제작되어야 한다.
8.2 화학공정용 열교환기
화학공정용 열교환기는 한국산업규격 KS B 6750 “압력용기(설계 및 제조일반)” 또는 미국 관형 열교환기 제작자 협회(TEMA) 규격(Standard of the tubular exchanger manufacturers association) 등의 최신판에 준하여 설계․제작되어야 한다.
미국 관형 열교환기 제작자 협회(TEMA) 규격에서 규정하는 유형별 적용 대상은 다음과 같으며 그 차이점은 <별표 1>과 같다.
(1) 정유 및 석유화학공정에서 사용되는 열교환기 : TEMA "R"형
(2) 화학공정에서 사용되는 열교환기 : TEMA "B"형
(3) 기타 일반공정에서 사용되는 열교환기 : TEMA "C"형
9. 설계조건
9.1 압력
(1) 최대운전압력이 게이지 압력으로 7 MPa(70 kgf/㎠) 이하인 열교환기의 설계압력은 최대운전압력에 최대운전압력의 10 % 또는 180 kPa(1.8 kgf/㎠) 중 큰 수치를 더한 수치이상으로 하여야 한다.(TEMA 기준에 따르는 경우
에는 최소설계압력은 520 kPa(5.3 kgf/㎠) 이상이어야 함.)
(2) 최대운전압력이 게이지 압력으로 7 MPa(70 kgf/㎠)를 초과하는 열교환기의 설계압력은 최대운전압력에 최대운전압력의 5 % 또는 700 kPa(7 kgf/㎠) 중 큰 수치를 더한 수치이상으로 하여야 한다. 다만, 파일럿 작동형(Pilot type) 안전밸브를 설치하는 경우에는 공정용기의 설계압력은 최대 운전압력에 최대운전압력의 5 %를 더한 수치 이상으로 할 수 있다
(3) 반응기의 인입측과 토출측의 유체를 열교환시키는 열교환기 등과 같이 동체측과 튜브측에 동시에 압력이 걸리는 열교환기로서 튜브 및 튜브판(Tube sheet)의 설계압력을 동체측과 튜브측의 압력차로 하는 경우에는 튜브 및 튜브판의 설계압력은 동체측과 튜브측의 예상되는 최대압력차에 최대운전압력의 10 % 또는 350 kPa(3.5 kgf/㎠) 중 큰 수치를 더한 수치이상으로 할 수 있다.
9.2 온도
(1) 일반적으로 열교환기의 설계온도는 최대운전온도에 30 ℃를 더한 수치로 한다.
(2) 냉각기 및 응축기의 냉각수측 설계온도는 일반적으로 90 ℃로 한다. 이 경우에 공정유체측의 운전온도는 일반 공업용수를 냉각수로 사용할 때에는 200 ℃, 바닷물을 냉각수로 사용할 때에는 150 ℃ 이하이어야 한다.
(3) 열교환기의 설계온도를 결정할때에는 설계온도가 플랜지의 호칭압력을 결정하는데 영향을 주므로 이를 고려하여야 한다.
(4) 수분이 포함된 가벼운 탄화수소가스, 황화수소 또는 이산화탄소를 압력하에서 15 ℃ 이하로 냉각시킬때에는 수화물 결정이 생성되어 열교환기를 막히게 하므로 이러한 공정가스는 열교환기에 인입되기 전에 건조시켜야 한다. 알콜, 글리콜 또는 암모니아를 첨가하면 이러한 현상을 방지할 수 있다.
9.3 재질 및 부식여유
(1) 일반적으로 일반탄소강 및 저합금 탄소강을 사용하는 열교환기의 압력을 받는 부위의 부식여유는 다음과 같다.
(가) TEMA “R”형 : 3 mm
(나) TEMA “B” 및 “C”형 : 1.5 mm
(2) 튜브에는 부식여유를 적용하지 아니하며 부식성이 있는 유체를 취급하는 경우에는 합금강을 사용한다.
(3) 튜브판의 부식여유는 튜브측 및 동체측 양측에 9.3의 (1)항에서 규정하는 부식여유를 주어야한다.
9.4 압력손실
(1) 응축기 (Condenser)및 냉각기(Cooler)의 냉각수측에서의 압력손실은 일반적으로 68.6 kPa(0.7 kgf/㎠)이내로 한다.
(2) 공정유체측의 열교환기에서의 압력손실은 일반적으로 39.2~196 kPa(0.4~2kgf/㎠) 범위내에서 그 시스템의 특성 및 압력에 따라 결성한다.
(3) 반응기의 인입측과 토출측의 유체를 서로 열교환시키는 열교환기에서의 압력손실은 열교환기 1개당 다음과 같이 한다.
(가) 저압인 경우 : 14.7 kPa(0.15 kgf/㎠) 정도
(나) 고압인 경우 : 34.3 kPa(0.35 kgf/㎠) 정도
(4) 상압 이상에서 운전되는 응축기의 공정 유체측의 압력손실은 9.8~34.3kPa (0.1~0.35 kgf/㎠) 범위내에서 결정한다.
(5) 재비기(Reboiler)의 공정유체측의 압력손실은 1.47~14.7 kPa(0.015~0.15kgf/㎠) 범위내에서 결정하며 특별히 열사이폰형 (Thermosyphon) 재비기의 공정 유체측의 압력손실은 1.47~3.43 kPa(0.015~0.035 kgf/㎠) 범위내에서 결정한다. 또한 일회통과형(Once-Through) 재비기의 공정유체측의 압력손실은14.7 kPa(0.15 kgf/㎠) 정도로 한다.
(6) 진공하에서 운전되는 응축기의 공정유체측의 압력손실은 10~25 mmHg 범위내에서 결정한다.
9.5 오염저항계수(Fouling resistance)
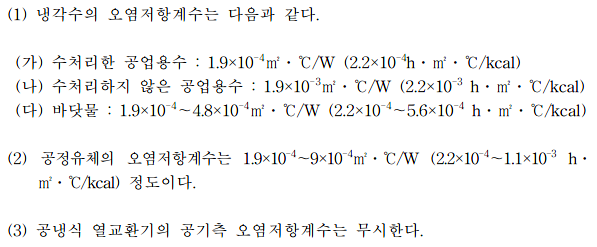
9.6 동체측 및 튜브측 유체의 선정
(1) 오염물질이 함유된 유체(Fouling fluid)는 튜브측으로 통과시킨다.
(2) 점도가 2 센티스톡스(cSt) 이상인 유체는 동체측으로 통과시킨다.
(3) 부유물질(Suspended solid)이 함유된 유체는 튜브측으로 통과시킨다.
(4) 고온의 유체는 튜브측으로 통과시킨다.
(5) 냉각수는 일반적으로 튜브측으로 통과시킨다.
(6) 부식성이 있는 유체는 튜브측으로 통과시킨다.
9.7 총괄열전달계수
(1) 응축기의 총괄열전달계수는 120~870 W/㎡․℃ (100~750 kcal/h․㎡․℃) 정도이다. 대부분의 탄화수소 응축기의 총괄열전달계수는 570 W/㎡․℃ (490 kcal/h․㎡․℃) 정도이다.
(2) 재비기의 총괄열전달계수는 290~580 W/㎡․℃ (250~500 kcal/h․㎡․℃) 정도이다.
(3) 액․액시스템 및 혼합상(Mixed phase) 시스템의 관형 열교환기에서의 총괄열전달계수는 290~410 W/㎡․℃ (250~350 kcal/h․㎡․℃) 정도이다.
(4) 가스․가스 열교환기에서의 총괄열전달계수는 80 W/㎡․℃ (70 kcal/h․㎡․℃) 정도이다.
(5) 이중관식 열교환기에서의 총괄열전달계수는 관형열교환기의 1/3 정도이다.
10. 열교환기의 형태
열교환기의 종류는 <별지그림 1>과 같이 여러 가지 형태가 있다.
제4장 가열로
11. 설계조건
11.1 설계압력
설계압력은 최대운전압력의 10 % 또는 180 kPa(1.8 kgf/㎠) 중 큰 값을 더한 수치이상으로 한다.
11.2 설계온도
튜브의 설계온도(Tube metal design temperature)는 그 금속의 최대사용허용온도 이하로 한다.
11.3 압력손실
가열로에서의 압력손실은 <표 1> 기준에 따른다.
<표 1> 압력손실 기준

11.4 튜브내의 유속
튜브 내에서의 유속은 <표 2> 기준에 따른다.
<표 2> 유속기준
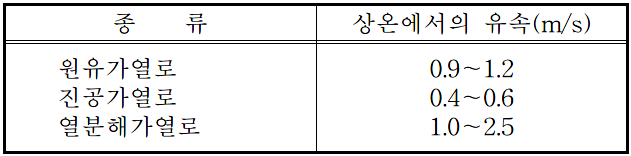
11.5 열 플럭스량(Heat flux rate)
(1) 용량이 1.45×106 W (1.25×106 kcal/h) 이하인 가열로의 복사부(Radiant section)에서의 플럭스량은 외부표면적 기준으로 16×103 ~26×103 W/㎡(14×103 ~22×103 kcal/㎡․h) 범위내에서 결정한다.
(2) 용량이 5.8×106 W (5×106 kcal/h) 이상으로 가운데 벽이 없는 가열로의 복사부에서의 플럭스량은 31×103 ~38×103 W/㎡ (27×103 ~33×103 kcal/㎡․h) 범위내에서 결정한다.
(3) 복사부에 가운데 벽이 있는 가열로는 앞에서 규정한 플럭스량의 120 %까지 허용된다.
11.6. 튜브의 크기
가열로에 사용하는 튜브의 지름은 파이프의 호칭 지름으로 DN 150(NPS 6) 이하를 주로 사용한다.
12. 가열로의 형태
가열로의 형태는 다음과 같다.
(1) 바닥연소식 수평튜브(Bottom fired horizontal tube-box)형
(2) 벽연소식 수평튜브(Wall fired horizontal tube-box)형
(3) 바닥연소식 수직튜브(Bottom fired vertical tube-box)형
(4) 벽연소식 수직튜브(Wall fired vertical tube-box)형
(5) 바닥연소식 수직튜브원통(Bottom fired vertical tube-cylindrical)형
(6) 지붕연소식 수직튜브원통(Down fired vertical tube-cylindrical)형
(7) 바닥연소식 나선튜브원통(Bottom fired spiral tube-cylindrical)형
(8) 지붕연소식 나선튜브원통(Down fired spiral tube-cylindrical)형
13. 버너의 종류
가열로용 버너의 종류에는 다음과 같은 것들이 있다.
(1) 가스전용 버너
(2) 액체전용 버너
(3) 가스․액체 겸용 버너
14. 가열로의 효율
14.1 효율
인입유체온도에 따른 일반적인 가열로의 효율은 <표 3>와 같다.
<표 3> 가열로의 효율
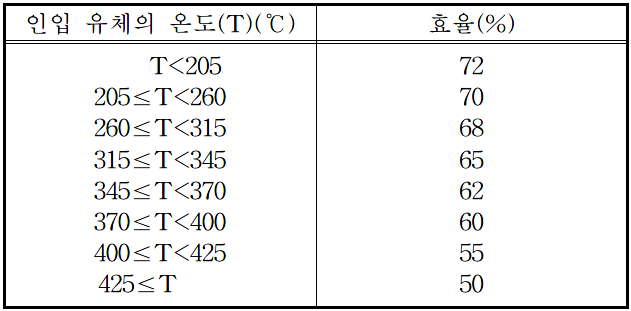
14.2 효율증대 방법
(1) 가열로의 효율을 증대시키는 방법에는 다음과 같은 것들이 있다.
(가) 대류부(Convection section)에 공정유체를 통과시키어 폐열을 회수하는 방법
(나) 대류부에서 스팀을 발생시키어 폐열을 회수하는 방법
(다) 연소가스와 연소용 공기를 열교환시키어 폐열을 회수하는 방법
(2) 가열로 설계시에는 제1항 각호의 방법을 복합적으로 사용하여 가능한 한효율을 높여야 한다.
제5장 펌프
15. 설계조건
15.1 용량
(1) 펌프의 설계 용량은 일반적으로 정상운전 유량의 115 %로 산정하며 최소한 110 % 이상으로 하여야 한다.
(2) 증류장치 등의 환류펌프은 설계용량은 정상운전유량의 125~135 %의 범위에서 산정하며 최소한 120 % 이상으로 하여야 한다.
15.2 펌프의 양정(Differential head)
(1) 펌프의 양정은 정상운전유량을 기준으로하여 산정한다. 그러나 유량의 변화가 큰 경우에는 높은 양정을 필요로하는 유량으로 산정한다.
(2) 보일러급수펌프의 양정은 미국국가기준협회규격 ANSI/ASME SectionⅠ"Power boiler" 의 기준에 따른다. 이 펌프는 안전밸브가 설정압력의 106%에서 작동될 때에도 정상운전 유량을 공급할 수 있어야 한다.
15.3 유효양정(NPSH)
(1) 펌프의 공정정보에는 시스템에서의 허용유효양정(NPSHa)이 포함되어 제공되어야 한다.
(2) 펌프는 어느 경우에도 시스템에서의 허용유효양정이 펌프의 제작자가 요구하는 유효양정(NPSHr)보다 커야한다.
(3) 허용유효양정은 다음과 같이 계산한다.

16. 펌프의 종류 및 선정기준
16.1 펌프의 종류
펌프의 종류는 <별지그림 2>와 같이 분류한다.
16.2 선정기준
(1) 다음의 경우 이외에는 일반적으로 원심펌프를 사용한다.
(가) 고양정 저용량인 경우 : 왕복동 펌프
(나) 유량이 1 ㎥/h이하인 경우 : 플런저 또는 다이아프람 펌프
(다) 유체의 점도가 1,000 cP 이상인 경우 : 기어 또는 스크류 펌프
(라) 유체에 고체입자가 포함되어 있는 경우 : 로브펌프
(마) 유체에 5 %(v) 이상의 기체가 포함되어 있는 경우 : 로타리 펌프
(바) 허용유효양정이 충분하지 않은 비점 액체를 취급하는 경우 : 수직형 캔(Can 또는 Barrel)형 원심펌프
(2) 형식별 일반설정 기준 및 장단점
(가) 왕복동펌프
① 다음의 경우에는 왕복동 펌프가 적합하다.
․유체의 점도가 큰 경우
․고양정이 필요한 경우
․일정 유량 또는 계량(Metering)이 필요한 경우
② 왕복동 펌프의 장단점은 다음과 같다.
․효율이 높다.
․마모성이 있는 유체를 취급하는 경우에는 사용할 수 없다.
․초기 투자비가 높다.
․유지․보수비가 높다.
․용량이 제한적이다.
․유량에 맥동(Pulsation)이 있다.
(나) 로타리펌프
① 다음의 경우에는 로타리펌프가 적합하다.
․허용유효양정이 작은 경우
․유체의 점도가 매우 큰 경우
② 로타리펌프의 장단점은 다음과 같다.
․고점도유체인 경우 효율이 높다.
․마모성이 있는 유체를 취급하는 경우에는 사용할 수 없다.(단, 로브펌프는 제외)
(다) 원심펌프
① 16.2의 (1)항에서 규정한 경우 이외에는 일반적으로 원심펌프가 적합하다.
② 원심펌프의 장단점은 다음과 같다.
․사용범위가 넓다.
․초기투자비가 낮다.
․허용유효양정에 제한을 많이 받는다.
․효율이 비교적 낮다.
․유지․보수비가 낮다.
제6장 압축기
17. 설계조건
17.1 용량
압축기의 설계용량은 일반적으로 정상운전시에 필요한 용량의 110 %로 한다.
17.2 압축비
최대 압축비는 단(Stage)당 3:1이하로 한다. 수소가스 승압(Boosting)용 압축기는 토출측에서의 온도가 150 ℃를 초과하지 않도록 압축비를 선정한다.
17.3 압축기의 양정(Head)
압축기의 양정은 일반적으로 정상운전 용량의 110 %를 기준으로하여 선정한다.
18. 예비압축기
18.1 왕복동식 압축기
(1) 일반적으로 연속공정에서는 예비압축기가 필요하다. 예비압축기의 용량도 주압축기의 용량과 크기를 동일하게 한다.
(2) 압축기는 다음 각호 중 하나의 방법을 선정하여 설치한다.
(가) 1대정상운전시 : 100 % 용량의 압축기 2대
(나) 2대정상운전시 : 50 % 용량의 압축기 3대
18.2 원심, 스크류 및 기어 압축기
(1) 일반적으로 예비 압축기를 설치하지 않는다.
(2) 이 경우에는 예비 로터(Rotor)를 확보하는 것이 좋다.
19. 압축기의 종류 및 선정기준
19.1 압축기의 종류
압축기의 종류는 <별지그림 3>과 같이 분류한다.
19.2 선정기준
19.2.1 공정 특성에 의한 종류별 적합성
공정의 특성에 의한 압축기의 선정 기준은 <표 4>와 같다.<표 4> 공정 특성에 의한 선정기준
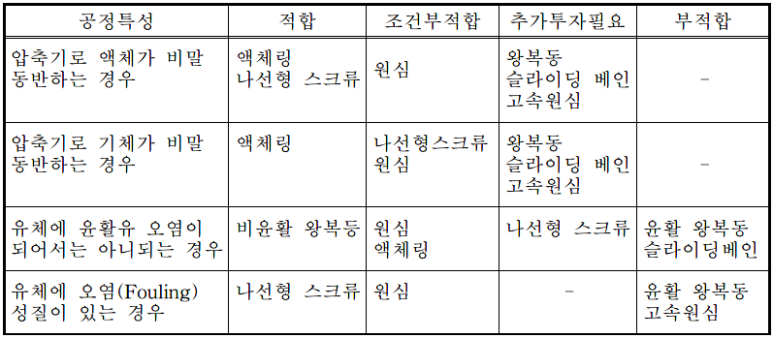
19.2.2 특수조건에 대한 적합성
특수한 조건에 의한 압축기 종류별 선정기준은 <표 5>와 같다.
<표 5> 특수 조건에 의한 선정기준
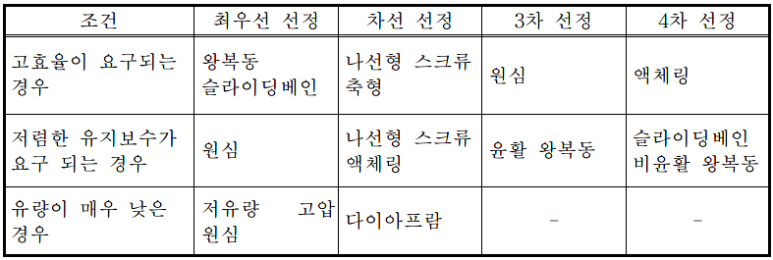
19.2.3 형식별 일반 선정기준 및 장단점
압축기의 형식별 일반적인 선정기준은 다음과 같다.
(1) 왕복동 압축기
(가) 사용범위
․압력 : 진공에서부터 약 690 MPa(7×103 kgf/㎠)까지
․유량 : 8.5~12,000 ㎥/h
․효율 : 80~90 %
(나) 장점
․토출압력이 매우높다.
․효율이 높다.
(다) 단점
․흐름에 맥동(Pulsation)이 있다.
․연속적인 운전을 위하여는 여유 압축기가 필요하다.
․부피가 크고 값이 비싸다
․유지보수비가 높다.
(2) 스크류 압축기
(가) 사용범위
․압력 : 게이지압력으로 약 1.8 MPa(18 kgf/㎠)까지
․유량 : 1.4×103 ~34×103 ㎥/h
․효율 : 75~85 %
(나) 장점
․유지보수비가 저렴하다.
․타르 및 폴리머가 함유된 유체에 사용할 수 있다.
․가격이 상대적으로 저렴하다.
(다) 단점
․토출압력이 낮다.
․소음이 크다
․유량의 변동 범위가 작다
․압축비가 제한적이다.
(3) 슬라이딩 베인 압축기
(가) 사용범위
․압력 : 게이지 압력으로 약 980 kPa(10 kgf/㎠)까지
․유량 : 85~10×103 ㎥/hr
․효율 : 60~75 %
(나) 장점
․가격이 상대적으로 저렴하다.
․유지보수비가 저렴하다.
(다) 단점
․토출압력이 낮다.
․유체가 윤활유에 오염되기 쉽다.
․깨끗한 유체에만 사용할 수 있다.
․효율이 낮다.
(4) 원심압축기
(가) 사용범위
․압력 : 35 MPa(350 kgf/㎠)까지
․유량 : 1.7×103 ~255×103 ㎥/h
․효율 : 68~76 %
(나) 장점
․유체가 윤활유에 오염될 가능성이 낮다.
․유지보수비가 저렴하다.
․왕복동 압축기에 비하여 가격이 저렴하다.
(다) 단점
․분자량이 적은 유체에 사용할 수 없다.
․저유량에서 사용할 수 없다.
제7장 배관
20. 설계 및 제작 규격
20.1 배관적용기준
배관은 KOSHA GUIDE “배관제작 및 설치에 관한 기술지침” 및 미국국가기준협회규격 ANSI/ASME B 31.3 “Chemical plant and petroleum refinery piping” 등의 최신판에 준하여 설계․제작․설치되어야 한다.
20.2 플랜지 적용기준
배관용 플랜지는 KOSHA GUIDE “플랜지 및 가스킷 등의 접합부에 관한 기술지침”, 미국국가기준협회규격 ANSI/ASME B 16.5 “Pipe flanges and flanged fittings” 등의 최신판에 준하여 설계․제작․설치되어야 한다.
21. 설계조건
21.1 압력
배관의 설계 압력은 그 배관이 연결되는 설비의 최대설계압력으로 한다.
21.2 온도
배관의 설계온도는 그 배관이 연결되는 설비의 최대설계온도로 한다.
21.3 압력손실 및 유속
(1) 액체배관에서의 압력손실은 배관내에서 액체가 기화되지 않아야 하며 또한 배관의 마모를 방지할 수 있는 범위내에서 결정한다.
(2) 기체 배관에서의 압력손실은 마모 및 소음을 방지할 수 있는 범위내에서 결정한다.
(3) 고체가 함유된 유체의 유속은 고체가 침전되지 않는 속도이어야 한다.
(4) 긴 액체 배관에서는 갑자기 밸브가 잠기었을 때에 햄머링(Hammering) 현상이 발생하지 않는 유속이하이어야 한다.
(5) 기체 배관에서의 유속은 음속이하이어야 한다.
(6) 기․액 혼합유체 배관에서의 유속은 슬러그 흐름(Slug flow)이 생성되지 않도록 충분한 속도를 유지하도록 한다.
(7) 압력손실 및 유속은 경제성을 감안하여 선정하여야 한다.
22. 플랜지의 형태
22.1 돌출면(Raised face) 플랜지
모든 공정용 배관에는 특별한 경우를 제외하고는 돌출면 플랜지를 사용한다.
22.2 링형(Ring type joint) 플랜지
링형 플랜지는 고온․고압의 유체를 취급하는 경우에 사용한다.
22.3 평면(Flat face) 플랜지
평면 플랜지는 물 및 공기․질소를 취급하는 배관에만 사용한다.
23. 볼트․너트
23.1 형태
모든 공정용 볼트는 스터드 볼트(Stud bolt)를 사용한다.
23.2 재질
(1) 540℃ 이하의 공정배관에 사용하는 볼트의 재질은 최소한 한국산업규격 KS D 3755 “고온합금강 볼트재”에서 규정하는 SNB7 (ASTM A-193 GR B7), 너트의 재질은 한국산업규격 KS D 3752 “기계구조용 탄소강재”에서 규정하는 SM45C (ASTM A-194 2H) 이상이어야 한다.
(2) 고온용 공정배관에는 그 온도에 적합한 합금강 재질을 사용하여야 한다.
24. 플랜지 및 가스킷
플랜지 및 가스킷의 사용온도 및 사용압력은 KOSHA GUIDE “플랜지 및 가스킷 등의 접합부에 관한 기술지침”에서 정하는 바에 따른다.
<별표 1> 미국 관형 열교환기 제작자 협회(TEMA) 형식별 차이점
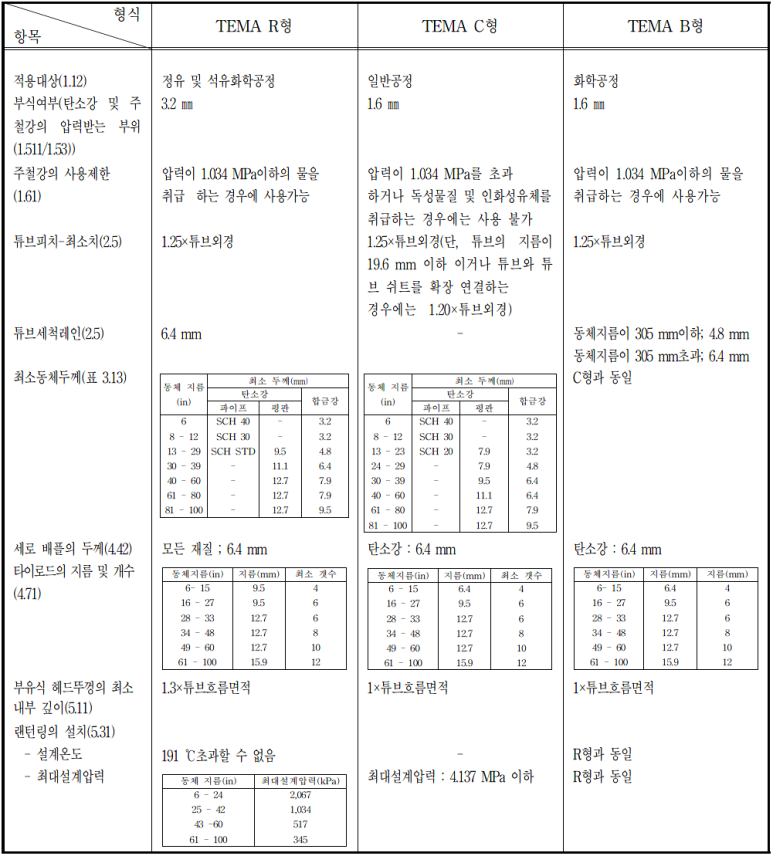
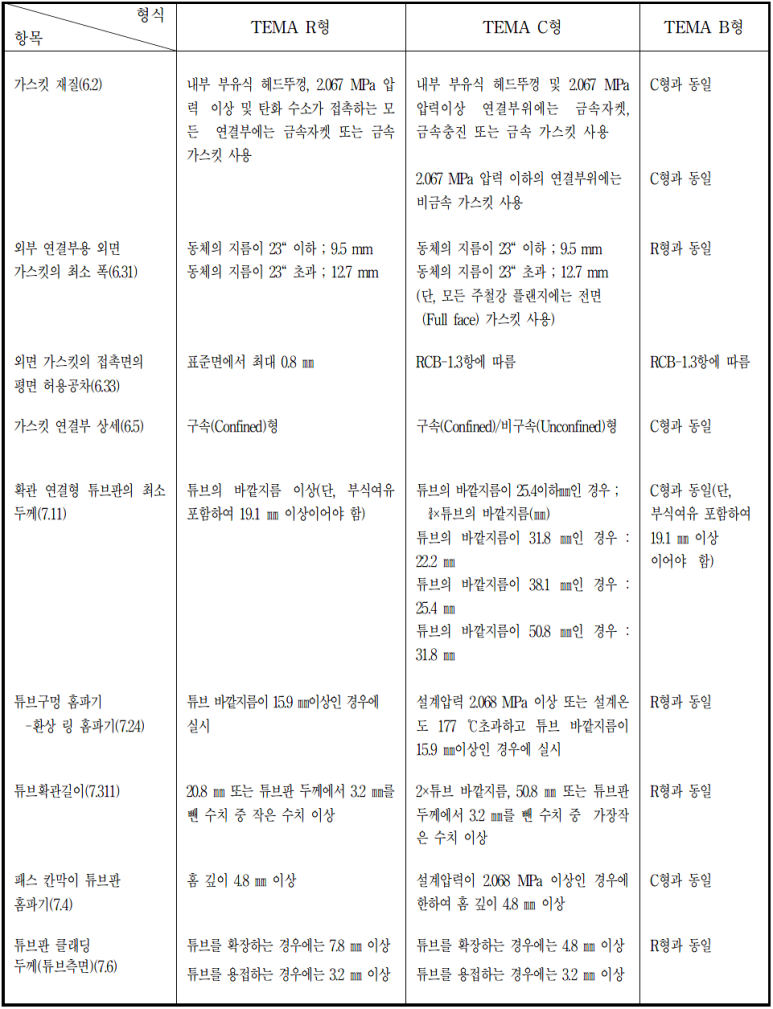
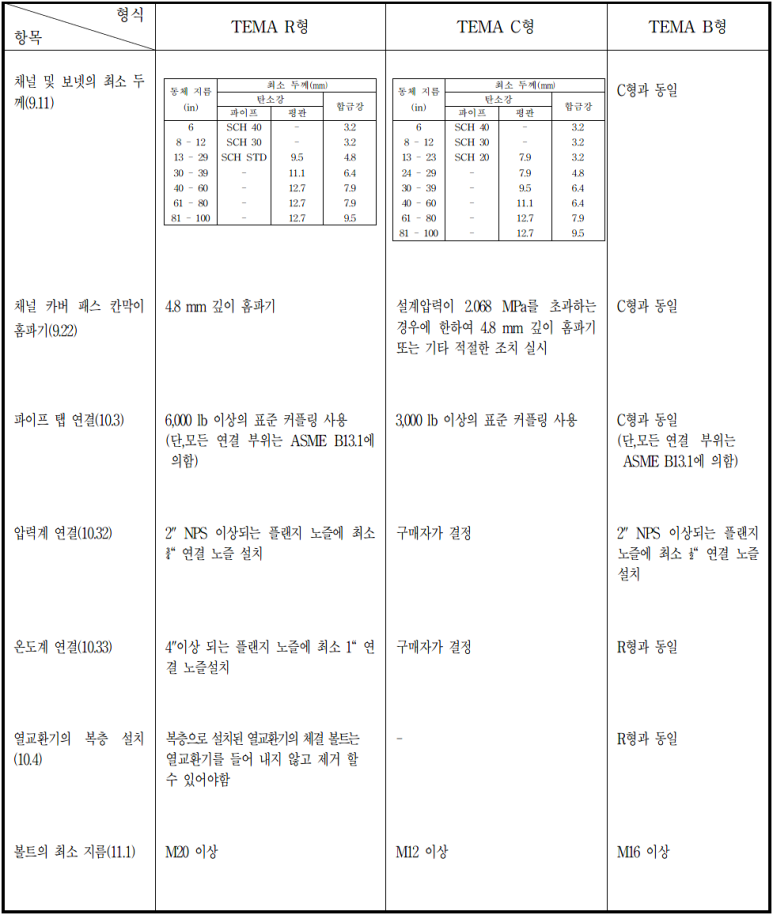
<별지그림 1> 열교환기의 형태
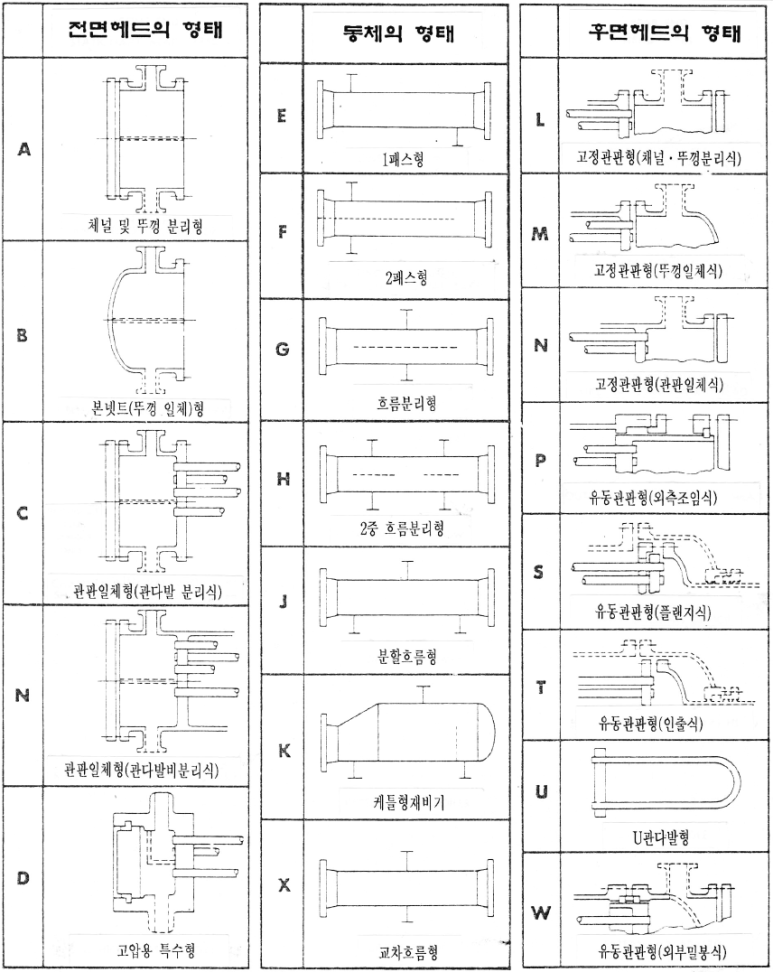
<별지그림 2> 펌프 계통도
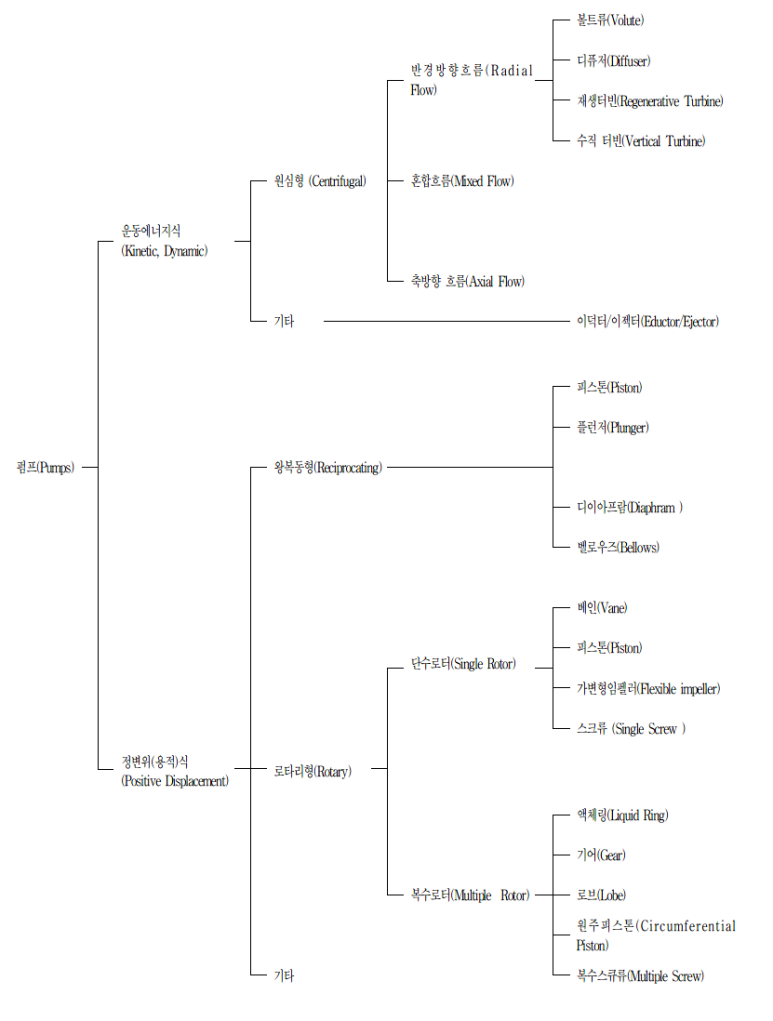
<별지그림 3> 압축기 계통도
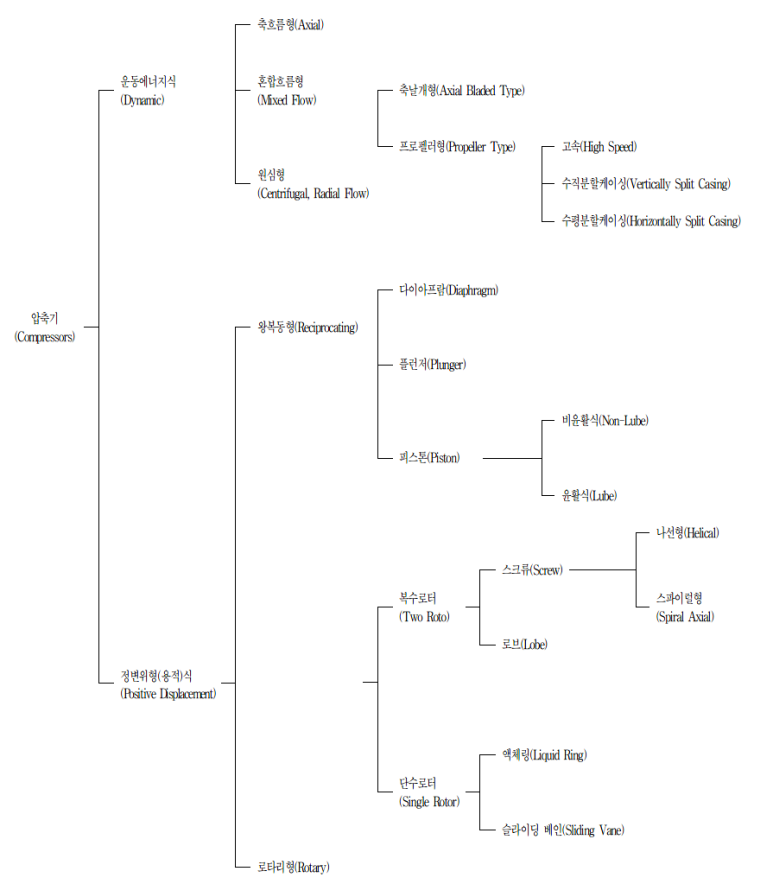
화학설비 등의 공정설계에 관한 기술지침(KOSHA GUIDE) - 2012.07
D - 37 - 2012 화학설비 등의 공정설계에 관한 기술지침(KOSHA GUIDE) - 2012.07 1. 목적 이 지...
blog.naver.com
'기준·규격 > 안전설계(D)' 카테고리의 다른 글
STKM - 기계 구조용 탄소 강관(KS D 3517 : 2008) (0) | 2023.03.07 |
---|---|
화학설비의 재질선정에 관한 기술지침(KOSHA GUIDE) - 2012.07 (0) | 2023.03.07 |
SGT - 일반 구조용 탄소 강관(KS D 3566 : 2018) (0) | 2023.03.05 |
TS - 압력용 경질 폴리염화비닐 이음관(KS M 3402 : 2021) - PVC (0) | 2023.03.05 |
SPPG - 연료 가스 배관용 탄소 강관(KS D 3631 :2020) (0) | 2023.03.05 |