석유화학공장의 염화수소 누출사고를 통한 대기벤트시스템의 안전성 향상 방안
A Study on the Safety Improvement in a Venting System from the HCl Release Accident of a Petrochemical Company
요약
이 논문은 2008년 5월 H 석유화학에서 발생한 염화수소 누출 사고에 대한 염화수소 누출량 및 피해 범위를 정량
적으로 산정하고 예방대책을 제시하는데 그 목적이 있다.
염화수소 Column의 안전밸브를 통해 누출된 양은 안전밸브 배출 용량, 이상상태방정식 및 기계적 에너지 수 지식을 사용하여 계산한 결과, 최소한 76.8 kg의 염화수소가 누출된 것을 알 수 있었다.
또한, PHAST 등의 프로그램을 활용하여 안전밸브 설치지점(높이 24 m)으로부터 약 350 m 떨어진 곳에서의 염화수소 농도를 예측한 결과, 지표면 누출로 가정하여 계산하는 ALOHA 및 K-CARM 프로그램에서는 각각 304 ppm과 1,700 ppm로 예측되었고 누출 높이에서의 지표면 값을 계산하는 PHAST 프로그램에서는 1 ppm 이하로 예측되었다.
위 결과는, 사고 당시 염화수소가 안전밸브를 통해 최소 76.8 kg이 누출되었고 누출 지점으로부터 약 350 m 떨어진 곳에 있던 근로자들이 1 ppm 이하의 농도의 HCl 가스에 폭로되었음을 말해준다. 또한, 이러한 사고를 예방하기 위해서는 염화수소와 같은 독성물질은 스크러버 등을 거쳐 세정 후 안전하게 대기로 배출(방출) 시켜야 한다는 사실을 제시한다.
I. 서론
화학공장 및 공정에서 발생되는 폐가스(off gas)는 일반적으로 연소/소각, 흡수/흡착 방법 등을 통해 안전하고 무해한 가스로 처리하여 대기로 배출시킨다. 또한, 이러한 처리시설을 거치지 않고 안전밸브의 방출관 또는 벤트스택(vent stack)을 이용하여 폐가스를 대기로 직접 분출시키기도 한다. 그렇지만 이렇게 폐가스를 대기로 직접 분출시킬 경우에는 지표면 착지 농도를 고려해야 한다. 즉, 가연성 물질의 경우는 지표면에 착지할 때의 농도가 폭발하한을 넘지 않아야 하고, 독성물질은 그 허용농도 이하로 충분히 희석되어야만 한다. 그렇지 않을 경우에는 지표면에 축적된 가연성 가스에 의해 대형 화재·폭발이, 독성가스에 의해 화학물질 중독사고가 발생할 수 있기 때문이다[1,2,3].
실제로 2008년, H석유화학에서 염화수소(HCl)가 대기로 직접 누출되어 약 350 m 떨어진 지점에서 작업하던 근로자가 구토 및 현기증을 일으켜 병원으로 후송된 사고가 발생하였다[4]. 따라서, 이 연구는 위 사고를 정량적으로 분석하여 실제로 누출된 염화수소의 양과 근로자에게 폭로 되었던 농도를 예측하여, 이러한 사고가 재발하지 않도록 하는데 그 목적이 있다.
II. 사고개요 및 원인
2.1. 사고사례 개요
2008년 5월 H석유화학에서 154 kV 수전시설의 낙뢰충격 보호장치(lightning arrestor) 소손으로 정전이 발생하였다. 이에, 관련 설비 등을 가동 정지하는 과정에서 HCl Column의 안전밸브를 통해 염화수소가 분출되어, 분출지점으로부터 350 m정도 떨어진 곳에서 작업하던 근로자 2명이 폭로되어 구토 및 현기증의 증상으로 병원으로 후송된 사고이다.
2.2. 사고원인물질
사고 원인물질은 HCl Column에서 분출된 무수염화수소(HCl)로서 주요 물성은 Table 1과 같다.
2.3. 사고설비
사고설비는 HCl Splitter Column 및 동 설비에 설치된 안전밸브이며, 사양은 Table 2, Table 3과 같다.
이때, 안전밸브를 통해 염화수소가 분출된 시간을 알기 위해 사고당시 HCl Column의 운전압력기록을 확인하였고 그 결과, 분출압력으로부터 분출 정지압력까지의 시간은 약 15초 이었다.
2.4. 사고발생공정
사고발생 공정은 Fig. 1과 같이 염소(Cl2)와 에틸렌(C2H4)을 반응시켜 경질물 제거, 수세척 및 수분제거 공정을 통해 EDC(ethylene dichloride)를 생산하고 다시 EDC 열분해공정을 통해 다음식과 같이VCM(vinyl chloride monomer)과 HCl로 분해시키는 공정이다.
CH2ClCH2Cl(EDC) →CH2CHCl(VCM) + HCl
1) TLV(Threshold Limit Values): ACGIH의 노출기준으로 근로자들이 보통평상시 작업할 때에 공기중의 농도가 근로자에게 큰 영향을 미치지 않는 농도
2) TWA(Time Weighted Average): 1일 8시간, 주 40시간 동안의 평균농도
3) STEL(Short Term Exposure Limits): 단시간 노출한계로, 노출 간격이 1시간 이상인 경우 1일 작업시간 동안 4회까지 노출이 허용되는 농도
4) ERPG(Emergency Response Planning Guideline)

Table 1. Properties of material related to accident

Table 2. Specification of HCl Column

Table 3. Specification of PSV

Fig. 1. Schematic diagram of accident process.
사고는 EDC 열분해 공정 후단의 HCl Splitter Column에서 발생하였다.
2.5. 사고발생원인
정전 발생으로 VCM공장이 가동 중지되었고 이후, HCl Splitter Column 응축기에 냉매 공급이 중단되었으며 이로 인해 HCl Splitter Column 내부의 압력이 상승하여 안전밸브의 작동으로 인해 무수 염화수소가 분출되었다.
보통, Column에서 압력이 상승할 경우 컨트롤 밸브가 작동하여 염화수소를 스크러버로 긴급 방출시킨다. 그렇지만, 사고 당시에는 계장용 공기의 공급 중단으로 컨트롤 밸브가 정상적으로 작동되지 않았고 이로 인해, Column의 압력이 상승하여 안전밸브가 작동하였고 염화수소가 곧바로 대기로 분출되었다.
III. 누출량 및 착지농도예측
3.1. 누출량 추정
누출량은 안전밸브 배출용량 기준, 이상상태방정식 기준 및 압력용기로부터 가스 누출식(기계적 에너지 수지식)을 적용하여 계산하였다.
(1) 안전밸브 배출용량 기준
Table 3에서 안전밸브의 정격용량은 23,865 kg/hr이고 안전밸브가 작동되어 분출 정지될 때 까지의 시간은 약 15초로서 그 양이 99.4 kg임을 알 수 있었다.
(2) 이상상태방정식 기준
Table 3과 같이 Column상부 안전밸브의 분출압력 (P1)은 10.56 kgf/cm2 이며, 분출정지압력(P2)은 8.59 kgf/cm2 이다. 이때, 누출량은 누출전 용기내에 있는 염화수소의 양에서 누출 후 용기 내에 남아 있는 양을 빼는 방식으로 식 1과 같이 구하였다.

(3) 기계적 에너지 수지식 기준
음속 또는 아음속 누출인지를 파악하기 위하여 식 2를 적용하였다[5,6].
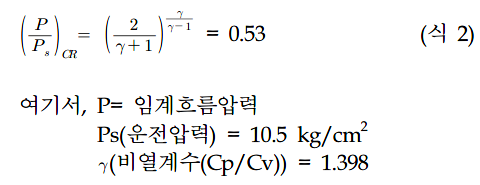
그 결과, 임계흐름압력비가 Pa(대기압)/Ps(운전압력보다 크므로 음속누출에 해당되고 음속누출에서의 누출량을 식 3으로 계산하였다.

위 3가지 식을 적용하여 누출량을 계산한 결과 누출량은 각각 99.4 kg, 129.5 kg 및 76.8 kg으로 산출
되었다. 즉, 사고를 통해 최소 76.8 kg이상의 염화수소가 누출된 것을 알 수 있었다.
3.2. 확산범위추정
확산범위를 추정하기 위해, ALOHA(미국환경보호청)(5.4.3), K-CARM(KOSHA)(2.4) 및 PHAST (DNV)(6.5.4) 프로그램을 사용하였고, 이를 근거로 누출지점에서 350 m 떨어진 곳에 있던 근로자에게 폭로된 염화수소의 농도를 추정하였다[7,8,9].

Table 4. Weather condition
(1) 대기상태(조건)
Table 4와 같은 사고당시 대기 조건 및 연속 누출(10분)을 가정하여 프로그램을 구동하였다. 단, 대기안정도는 F(매우 안정)로 가정하였다.
(2) ALOHA(5.4.3) 프로그램 결과
ALOHA(5.4.3) 프로그램을 구동한 결과 Table 5 와 같은 결과가 나왔다.
위 결과는 무수염화수소가 지표면에서 누출되었을 경우를 가정하여 나타낸 결과로서, 바람이 누출지점부터 근로자가 떨어진 지점으로 곧바로 불 경우 근로자는 약 304 ppm의 농도에 폭로될 수 있다는 것을 의미한다. 하지만 위 프로그램은 일정높이에서의 누출이 아닌 지표면에서의 누출을 가정하여 예측하기 때문에 일정 높이(24 m)에서 누출 후, 지표면에 도달 했을 때의 농도는 위의 값보다는 훨씬 더 낮을 것으로 예측된다.

Table 5. Result of ALOHA program
(3) K-CARM(2.4) 프로그램 결과
위 결과 또한, 지표면에서 누출된 것을 가정하여 결과를 예측한 것으로서, 분출 지점으로부터 350 m 떨어진 곳의 염화수소의 농도는 약 1,700 ppm으로서 ALOHA 프로그램의 결과 값보다는 3배 이상 높게 예측되었다. 하지만 위 프로그램 역시 염화수소가 지표면에서 누출했을 때의 결과로서, 실제 24 m 높이에서 분출된 염화수소가 지표면에 도달할 때는 대부분 확산되고 그 농도값은 위의 값보다는 낮을 것으로 예측된다.

Table 6. Result of K-CARM program
(4) PHAST(6.5.4) 프로그램 결과
염화수소 분출 높이(안전밸브 후단)에서 근로자가 위치한 곳까지의 염화수소의 농도를 예측하기 위해서 PHAST(6.5.4) 프로그램을 구동한 결과, Fig 2와 같은 결과를 얻을 수 있었다.

Fig 2. HCl Concentration grape.
염화수소 분출 후, 거리 350 m(근로자 위치), 높이10 m에서의 HCl의 농도값은 1 ppm 이었다. 이는, 사고당시 근로자에게 폭로된 염화수소의 농도가 1ppm이하라는 사실을 말해 준다. 또한 이 보다 높은 농도의 염화수소는 Table 7과 같이 근로자가 위치한 높이보다 훨씬 높은 곳에서 형성되어, 근로자가 직접적으로 폭로되지 않았음을 알 수 있다.
3.3. 동종재해예방대책
(1) 안전밸브 후단은 스크러버로 연결
염화수소와 같이 허용농도가 낮은 독성물질을 취급하는 공정의 안전밸브 토출측은 스크러버에 연결하여 세정 후, 대기로 안전하게 배출(방출) 시켜야 한다.
(2) 계장용 공기 시스템 보완
HCl Splitter Column의 내부 압력 상승시 스크러버로 긴급 방출할 수 있는 조절밸브의 계장용 공기가 차단되지 않고 지속적으로 공급되도록 비상전원에 연결하거나 30분 이상 공급 가능한 계장용 공기 저장탱크를 설치하여야 한다.

Table 7. Result of PHAST program
Ⅵ. 결론
이 연구는 2008년에 발생한 염화수소 누출사고에 대하여 염화수소 누출량 및 확산범위를 예측하고, 이러한 벤트 시스템의 안전성 향상 방안을 제시하였다.
안전밸브 작동으로 인해 15초 동안 누출된 HCl량은 최소한 76.8 kg 이상이었고, 거리 350 m에서의 농도는 ALOHA 프로그램의 경우는 304 ppm, K-CARM 프로그램은 1,700 ppm의 농도가 형성된 것으로 예측되었다.
이는 실제 분출높이(24 m)에서의 누출이 아닌, 지표면 누출을 가정한 값으로서 실제 높이에서 누출된 염화수소가 지표면에 도착할 때의 농도는 그보다 훨씬 낮을 것으로 추정할 수 있다. 실제 분출 높이에서 확산 후, 지표면의 농도를 예측할 수 있는 PHAST 프로그램을 구동한 결과, 근로자가 위치한 높이에서의 염화수소의 농도는 1 ppm
이하이고, 150 ppm이상의 고농도는 근로자 위치로 부터 높이 50 m이상에서 형성되는 것을 알 수 있었다. 비록 낮은 농도라도 염화수소의 허용농도(TLV,1 ppm)가 매우 낮기 때문에[10], 근로자들에게 구토 및 현기증과 같은 증상을 일으킬 수 있다고 판단된다.
이러한 사고를 예방하기 위해서는 염화수소와 같은 독성물질을 취급하는 공정의 안전밸브 후단은 반드시 스크러버로 연결하여 안전하게 처리하는 것이 중요하고 또한, 내부 압력 상승시에 스크러버로 긴급 방출할 수 있는 조절밸브의 계장용 공기가 차단되지 않도록 비상전원 등에 연결하는 것이 필요하다는 것을 알 수 있다.
참고문헌
[1] KOSHA Code D-39, “수소 벤트스택 및 벤트 배관의 공정설계 지침", 한국산업안전보건공단, (2005)
[2] API Standard 521 7.3.4, "Vent stacks", (2000)
[3] KOSHA Code P-37, “최악의 누출시나리오 선정지침”, 한국산업안전보건공단, (2005)
[4] 중대산업사고 조사보고서, 한국산업안전보건공단, (2008)
[5] KOSHA Code P-14, “누출원 모델링에 관한 기술 지침”, 한국산업안전보건공단, (2000)
[6] 이영순 등, “화공안전공학”, pp 101-106, (1994)
[7] 미국환경보호청, “ALOHA 5.4.3”
[8] DNV, "PHAST 6.5.4"
[9] 한국산업안전보건공단, “K-CARM 2.4”
[10] 한국산업안전보건공단, “HCl MSDS", (2011)
석유화학공장의 염화수소 누출사고를 통한 대기벤트시스템의 안전성 향상 방안
석유화학공장의 염화수소 누출사고를 통한 대기벤트시스템의 안전성 향상 방안 A Study on the Safety ...
blog.naver.com
'공학 > 화학공학' 카테고리의 다른 글
도시가스(LNG) 중량환산 방법 (0) | 2023.04.10 |
---|---|
전량식(full bore)/양정식(Iift) 안전밸브 정의 및 설명 (0) | 2023.04.10 |
HAZOP 기법 (0) | 2023.04.10 |
수증기 폭발 (0) | 2023.04.10 |
ALOHA(Areal Location of Hazardous Atmospheres) 프로그램 사용법 (2) | 2023.04.10 |